Manufacturing errors and unplanned downtime are potentially very costly. The 2022 “The True Cost of Downtime” report found that manufacturers lost $1 trillion in manufacturing failures accounting for 11% of their yearly turnover.
And human error is worse in the manufacturing industry compared to other sectors. 23% of all unplanned downtime in manufacturing is the result of human error, compared with rates as low as 9% in other sectors.
Manufacturing errors can lead to product defects, increased costs, and damage to brand reputation. Implementing effective strategies to reduce errors not only improves product quality but also improves efficiency and overall profitability.
In this blog post, we will explore some proven strategies that manufacturers can adopt to minimize errors.
Invest in Employee Training
One of the key strategies for reducing manufacturing errors is having a well-trained workforce.
Provide comprehensive training programs for all employees involved in the manufacturing process. Continuous training ensures that employees are up to date with the latest technologies, procedures, and quality standards.
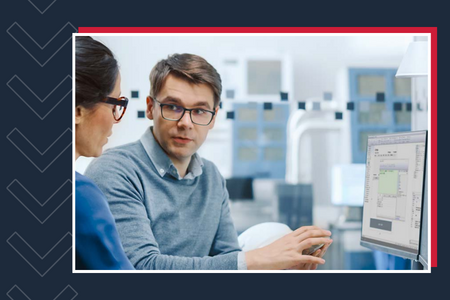
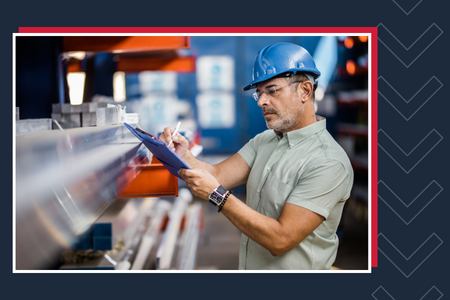
Implement Robust Quality Control Systems
Having rigorous quality control measures is essential for identifying and correcting errors at different stages of production.
Implementing a comprehensive quality management system can help identify the root causes of errors and streamline processes for optimal efficiency.
Use Digital Manufacturing Technologies
Integrating digital technologies, such as automation, artificial intelligence, CPQ, and machine learning, can significantly reduce the likelihood of errors.
Automated systems perform repetitive tasks with accuracy, minimizing the risk of human error. CPQ for Manufacturing (CPQM) solutions enable manufacturers to streamline the manufacturing processes for products with multiple configuration options, reducing error rates and improving production efficiencies.
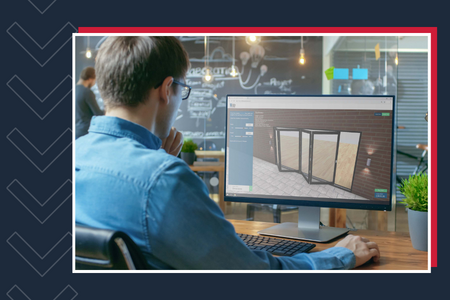
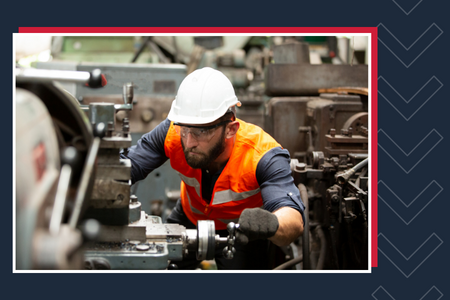
Regular Equipment Maintenance
Equipment failure can be a significant source of manufacturing errors.
Implement a proactive maintenance schedule to ensure that all machinery is operating at peak efficiency. Regular inspections and replacement of worn-out parts can prevent unexpected breakdowns and errors.
Supplier Collaboration
Work closely with suppliers to ensure the quality of incoming materials. Establish clear specifications and standards for raw materials, and regularly audit suppliers to verify compliance.
Working with trusted suppliers reduces the likelihood of errors caused by poor-quality materials.
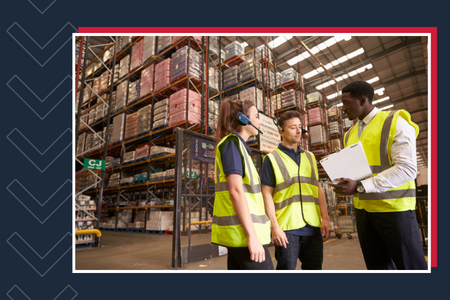
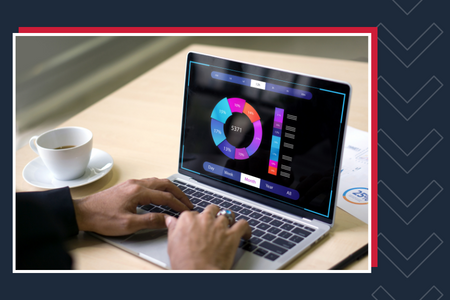
Data-Driven Decision Making
Use data analytics to monitor key performance indicators (KPIs) and identify areas for improvement.
Analyzing production data can provide insights into patterns and trends that may identify underlying issues leading to errors. Data-driven decision-making enables proactive problem-solving and continuous process improvement.
3D Product Visualization
Implement 3D product configurators to enable customers to configure and visualize their customized product selection within a pre-defined set of manufacturable parameters. This ensures that custom options are valid and reduces requote rates and manufacturing errors.
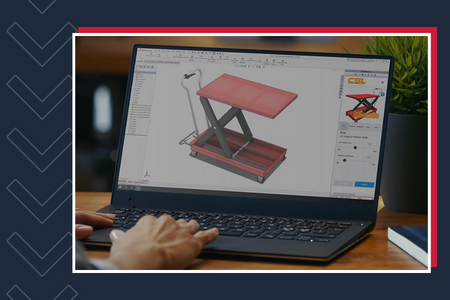
An effective strategy for reducing manufacturing errors encompasses both sales and production processes. Embracing a commitment to error reduction is a key step towards achieving excellence in smart manufacturing.
By implementing these proven strategies, manufacturers can improve product quality, reduce costs, and increase efficiency.
DriveWorks Technology Solutions for Reducing Manufacturing Errors
DriveWorks CPQ for Manufacturing software enables businesses to reduce sales and manufacturing errors with:
- Guided selling helps customers and guarantees valid configurations that can be manufactured
- 3D visualization that communicates complex design details effectively
- Integration with CAD to automatically create technical documents and manufacturing data