Manufacturers and engineers across all sectors are pulling together to provide solutions to help the on-going global pandemic.
Coronavirus has had an impact across the world and whilst it’s a hard time for everyone, in the midst of the chaos and disruption, we have seen people coming together and making a real difference.
There has been an incredible response from manufacturers, businesses and individuals everywhere. Communities have come together to utilise their design and manufacturing capabilities to help in the fight against COVID-19.
With such high levels of demand for the right equipment, supply chains have been disrupted and hospitals are running low on important supplies.
Meanwhile, manufacturers of non-essential items have seen a huge decline in demand for their products and have been forced to slow down or even stop production. These manufacturers have been putting their people, equipment, skills and time to good use and turned to producing vital equipment and products.
Using specialist skills, equipment and technology, engineering teams are developing and manufacturing urgently needed machinery, personal protective equipment (PPE) and other essential supplies.
From 3D printing protective masks, face shields and nasal swabs, to manufacturing ventilators and producing hand sanitizer, manufacturers are coming together to do all they can.
Industries Uniting
PPE has now become essential for many workers and individuals, and more important than ever before for medical staff. There has been an estimated 1000% global increase in demand for PPE in the past few weeks. There is also a desperate need for more ventilators across the world.
The World Health Organisation (WHO) has called on industry and governments to increase manufacturing to meet the rising global demand.
Working together, governments, industries and the Pandemic Supply Chain Network are boosting production and securing allocations for critically affected and at-risk countries.
There has been an amazing response to the government call for help to build ventilators, provide PPE and manufacture COVID-19 tests from a wide range of industries.
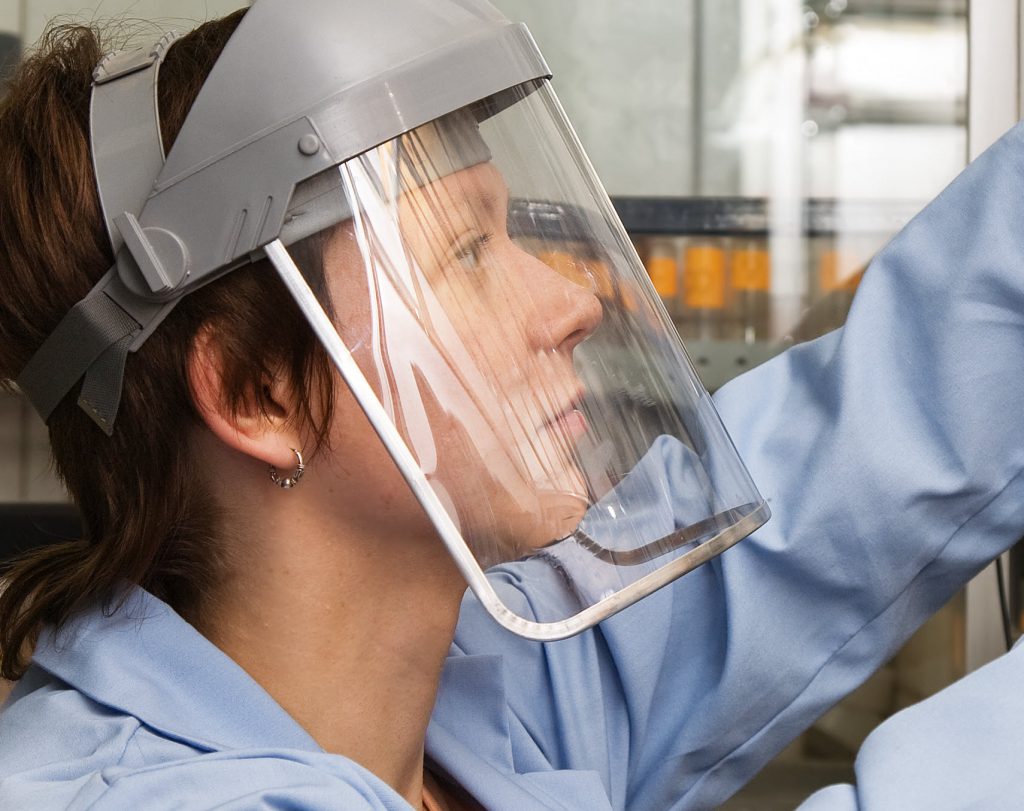
Leading companies in the aerospace, automotive, medical devices and motorsport sectors have come together and formed the VentilatorChallengeUK consortium. The consortium includes many companies, including Airbus, Rolls-Royce and McLaren.
They began working together to produce 10 years’ worth of ventilator production in just 10 weeks.
Advanced material engineer, Tecman, based in the West Midlands, has ramped up production of face shields to over 1 million each week after developing a disposable face shield to provide vital protection for healthcare staff.
Swedish air filtration manufacturer, Camfil are working with Swedish Heath Services to produce respiratory protection masks. They are currently delivering an incredible 100,000 protection masks each week. In total, they plan to provide 5 million masks for frontline workers.
It’s not just ventilators and PPE that’s been in high demand. Warrington wire company, Locker Group is also joining the fight against coronavirus by producing critical components including Nickel Wirecloth filters for ventilators and mesh which is used to create faraday cages to protect equipment at Great Ormond Street Hospital.
Over the past few months, we have heard many inspiring stories of companies of all shapes and sizes who are using their knowledge, skills and facilities to rise against the challenge of this global pandemic.
In many industries, manufacturers and engineers have moved quickly, switching from their usual production to designing, producing and delivering the urgently needed equipment to meet the growing demand.
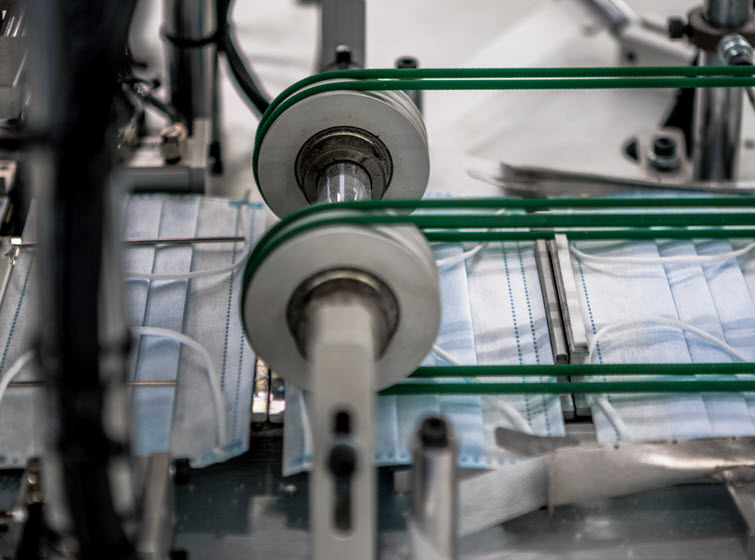
Bentley Motors, Aston Martin, Rolls Royce, Tesla and Nissan are all car manufacturers who have repurposed their production lines to help in the fight against COVID-19. Switching from car manufacturing to using their facilities to build and produce ventilators, visors and medical gowns.
BrewDog and Manchester Gin have both repurposed their distilleries to produce hand sanitiser in response to the national shortage. BrewDog has now packed and donated over 50,000 units to the NHS and local charities.
US-based SOLIDWORKS and DriveWorks reseller DesignPoint have been using their design skill set, vast network and 3D printing technology to deliver 2,300 face shields, 200 masks and 435 3D printed headbands across the country. DesignPoint has even provided STL files and resources so that people can print the equipment from anywhere.
FIRST have a community of volunteers and students all over the world who have been pulling together and doing whatever they can to make a difference. While the annual FIRST Robotics Championship events have been cancelled, FIRST teams and volunteers have been 3D-printing PPE for workers on the front line and even using their robots to deliver groceries to the elderly.
Before medical equipment can be purchased or donated to the government and NHS it must pass health and safety checks and meet essential safety requirements.
The Royal Mint organisation who typically produces coins are just one of many who have begun mass manufacturing medically approved visors for the NHS. They developed a successful prototype and got it approved in just 48 hours!
Composite Integration, based in Cornwall, is utilising its design and manufacturing capabilities to produce prototype face visors which have been reviewed and accepted by NHS Plymouth. They aim to manufacture approximately 2,500 visors a week for key workers.
Developing, testing and passing quality checks are activities that would normally take manufacturers months, but are now being achieved in just a matter of days and weeks.
AE Aerospace who supply high-quality precision machined components, worked around the clock to produce 6,000 complex ventilator parts in less than 2 weeks of receiving a drawing.
Vacuum maker Dyson developed a new ventilator in just 30 days using components from one of their current vacuum designs. Although they are no longer required in the UK, they may yet help the response in other countries.
Italian engineering start-up company, Isinnova began 3D printing essential life-saving valves used in respirators just 6 hours after hearing about a shortage in the local hospital. Since then, they have continued to develop other medical equipment including emergency masks for hospital ventilators.
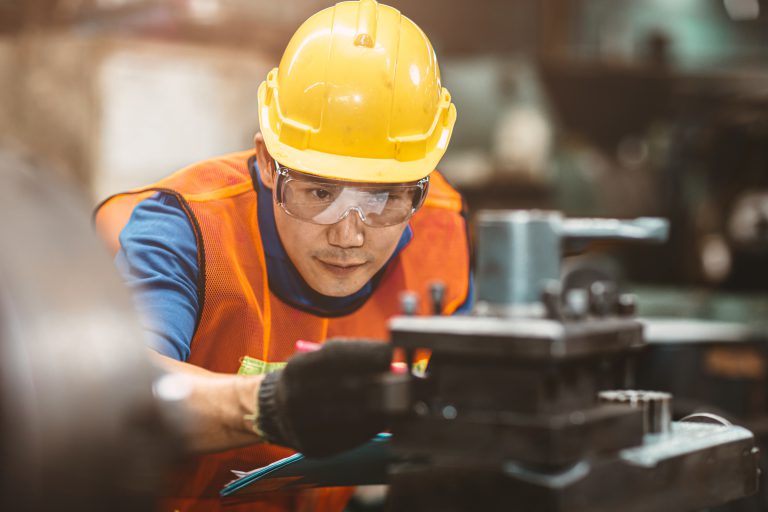
The Power of 3D Printing
Technology is playing a huge part in the battle against COVID-19 enabling manufacturers to rapidly switch and upscale production.
Complex parts can now be made anywhere with the power of advanced digital design and 3D printing.
Production times can be cut down, allowing manufactures to respond to sudden demand.
Manufacturers are quickly and cheaply develop and printing vital parts much faster than before.
3D printer manufacturer Formlabs is using 250 printers in its Ohio factory to manufacture 100,000 nasal swabs for COVID-19 testing each day.
HP and Markforged have made validated design files for many of the parts that do not require complex assembly freely available to download. Markforged customers and partners have printed over 3,200 face shields to date.
Dassault Systèmes’ 3DEXPERIENCE Lab has launched multiple initiatives so that a wide community of designers, engineers, scientists, makers and others can rapidly source, qualify, design, engineer and manufacture solutions to benefit local hospitals during the pandemic.
By making this information openly available, a community of engineers and designers are able to come together and produce PPE at the same time, in different cities and locations around the world. This community are sharing their CAD models and many are volunteering their time and effort to produce urgently needed protective equipment for health care workers.
3D printing has helped ease the strain on hospitals and offered a solution to relieve the pressure on supply chains. It has shown that having a diverse and adaptable global supply chain is essential and something that in the future could continue to save lives when major disruption happens.
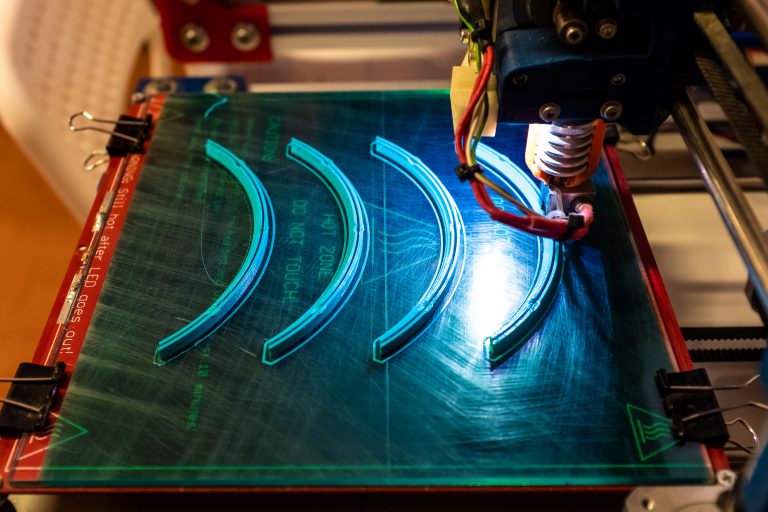
Working Together
Across all sectors, companies are uniting in a way that has never been seen before.
Companies who already manufacture medical equipment are expanding their production capacity to fulfil the demand in hospitals, while others are using their skills and resources to switch production.
Whilst these manufacturers are working hard to keep the supplies going, businesses, schools, colleges, universities and other groups are all stepping in to help their community.
Whether it’s using access to 3D printers to make face shields, or sewing aprons and face masks to donate to local care workers, there has been an overwhelming amount of support for those on the front line from members of the community and throughout the manufacturing industry.
Embracing Change
During this pandemic, there has been lots of change, but change isn’t always bad.
The manufacturers, communities and individuals who have pulled together to make us all stronger during this pandemic have proved that being agile and open to change is vital.
It’s become clearer than ever that companies who adapt, embrace change and move quickly are more likely to thrive.
There are so many great examples of companies who have adapted what they do. Companies who previously supplied pubs and bars with beer, and as demand declined, they adapted and made hand sanitiser instead. Not only have they provided the country with much-needed supplies and made a difference, but they are also keeping themselves afloat and keeping their staff employed.
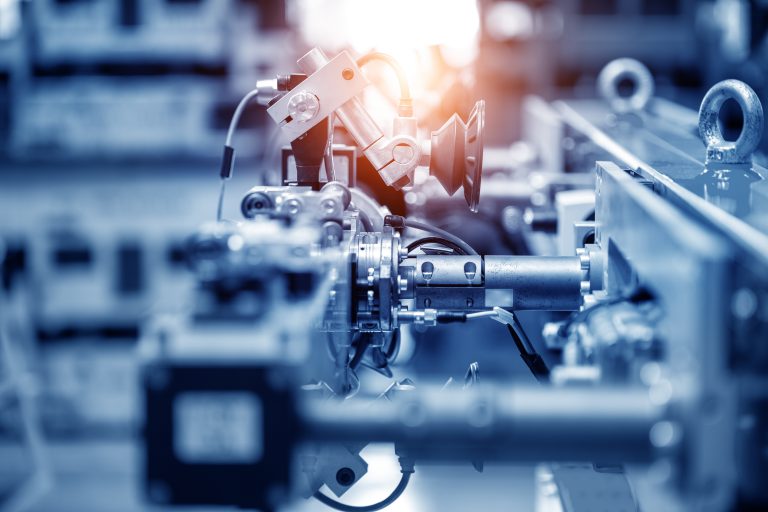
At DriveWorks, we are champions for change.
We’ve embraced digital transformation and almost everything we do is now digital. We use our own software to manage our data, create licenses for our customers and manage purchase orders, and even book annual leave, submit expenses and order fish and chips on a Friday.
Our digital processes and investments in technology have made transitioning to home working much smoother.
In work and in our personal lives, everyone across the world has been using technology more. Whether it’s doing an online food shop, a weekly team meeting, or a virtual pub quiz with family and friends, now more than ever, technology connects the world.
Digital transformation is essential – businesses need to embrace digital now, to be stronger tomorrow.
Look out for DriveWorks CEO, Glen Smith in this month’s DEVELOP3D Magazine talking about why we all need to be champions for change. Read it online for free.