Creating a 3D Printed Phone Holder Configurator
Every year we take on placement students across many of our teams. We’ve always valued the importance of investing in new talent and supporting the future of digital, and this past year has been no different.
Back in July 2020, 4 new interns joined our team.
We welcomed Ryan, Abi and Jacob to our Technical Team, and Sophie to our Sales & Marketing Team.
During Sophie’s placement, she took on lots of different tasks, including designing and developing a Phone Holder Configurator.
Through thorough research and experimenting with different methods of 3D printing, Sophie developed a configurator that could be used to configure custom phone holders that are the same but different.
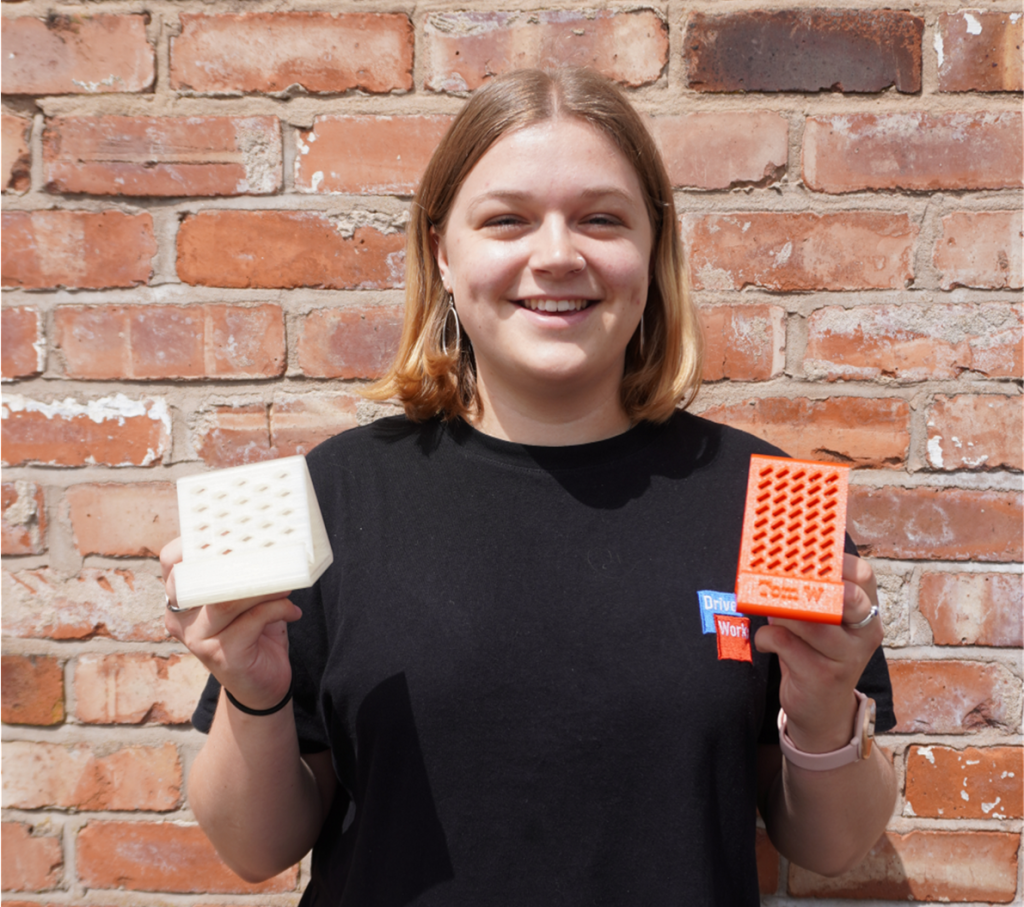
3D Printing Project Brief
The goal of the project was to create a new Example Configurator for DriveWorksLive.com demonstrating how DriveWorks can be used to generate 3D printing manufacturing data for highly customizable consumer products.
Developing a New Product
Sophie had done 3D printing during her Product Design course at the University of Leeds but she wanted to do some more research before getting started. Sophie wanted to find out exactly what the limitations of 3D printing can be.
Once Sophie had compiled her research, she then took the brief and turned both into a set of design requirements for the product.
She was left with a list of requirements for the 3D printing project:
- Must include organic shapes to show off 3D printing capabilities
- Must be highly driveable
- Must be suitable for a large range of different DriveWorks Live users
- Must be safe to use
- Overhangs greater than 45 degrees and bridges greater than 5mm must include support material
- Volume of support material should be minimised to keep cost and post-processing down
- Must fit on 3D printer bed (include a custom input on form or make suitable for standard home printers)
- Must be suitable for all standard 3D printing polymers
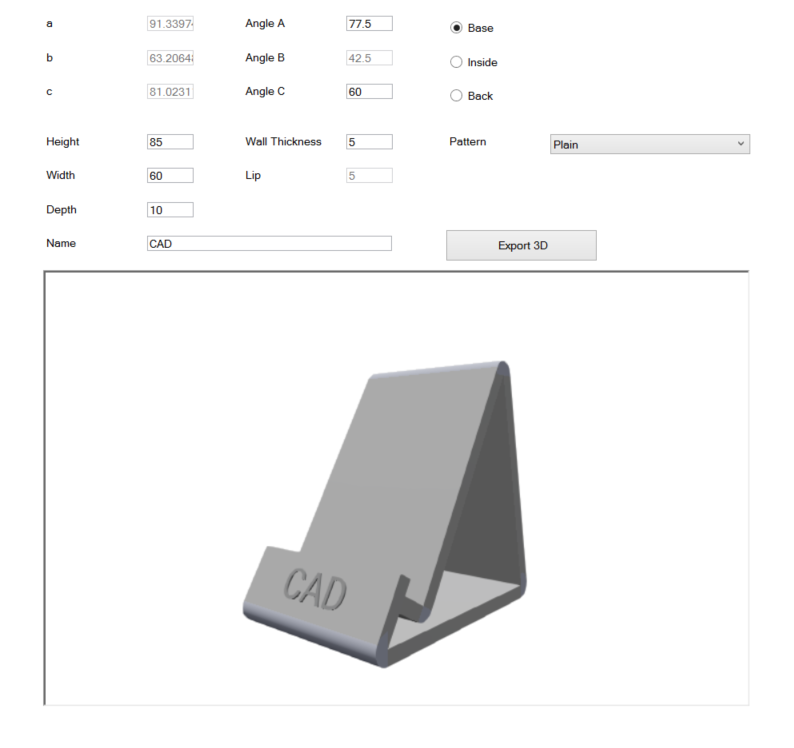
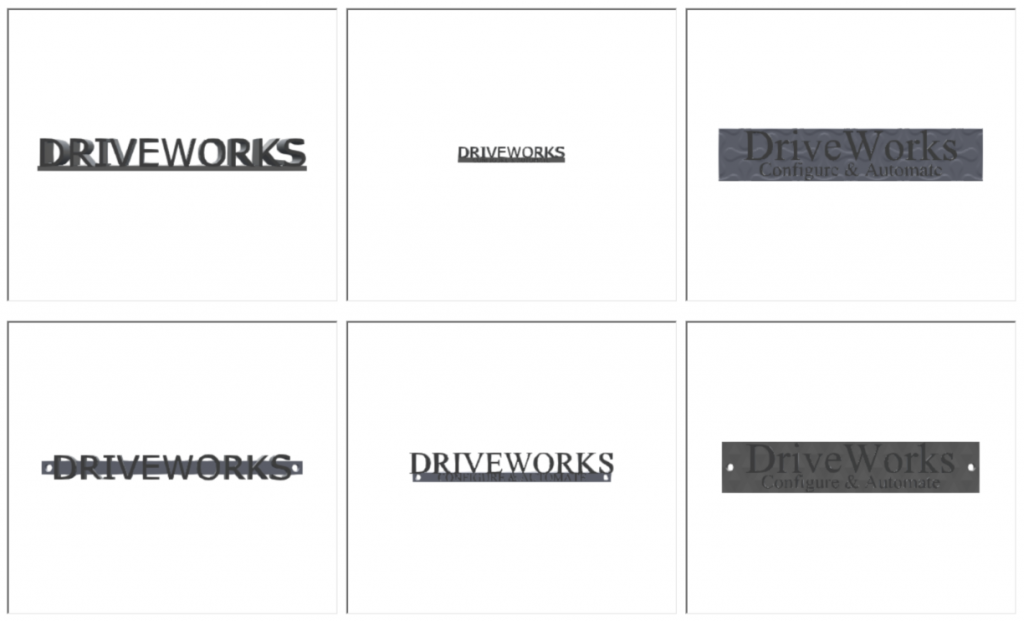
To deliver the brief Sophie made sure that some of the features on the phone stand were customizable. These customizable features included:
- Device height, depth and width
- Text font and value
- Mesh pattern on the surface
- Device resting angle
- Wall thickness
To ensure that there was as little re-work as possible, Sophie also took the time to do some testing at this point.
Building a Simple DriveWorks Configurator
The next task for Sophie was to build a simple one form DriveWorks configurator with a 3D preview of the product, and all the Form Controls required to configure it.
The purpose of this was to ensure the product could be configured and the required inputs were known before thinking about the appearance.
Sophie had to drive the model inside a 3D document which presented a design limitation.
It would have required many replacement models to keep the mesh pattern the same for all possible phone stand dimensions which would have resulted in the configurator being very slow.
Instead, Sophie designed the mesh pattern parts of the phone stand to have maximum overhangs of 45 degrees for the widest, shortest possible phone stand configuration.
This meant that any other configuration would stretch the pattern to have overhangs less than 45 degrees making it possible to print all configurations with no support material.
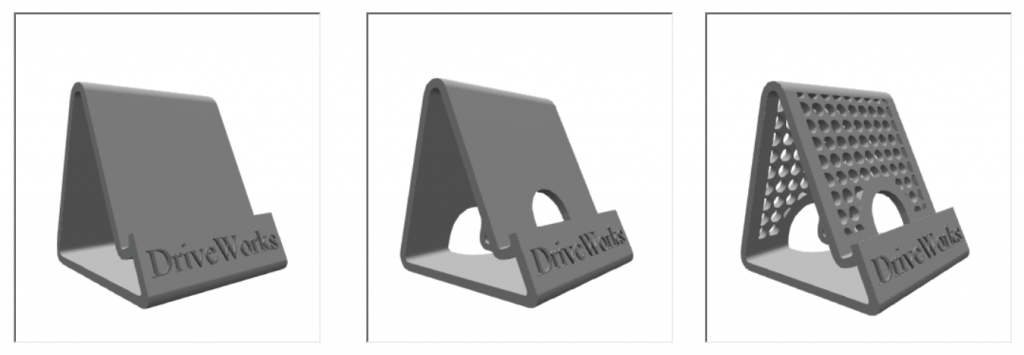
Developing the Configurator’s UI in Adobe XD
Next, Sophie then used Adobe XD to mock-up the design of the configurator. Sophie found this useful to make quick changes to the UI.
It is also possible to export assets straight from Adobe XD for use in a DriveWorks configurator. By creating a working Adobe XD prototype, Sophie was able to test the UX she had created and also show it to other members of the DriveWorks team for feedback.
Creating the Configurator
The final stage was to implement the UX created in Adobe XD into a DriveWorks project. This process was much quicker than it would have been without the prototype.
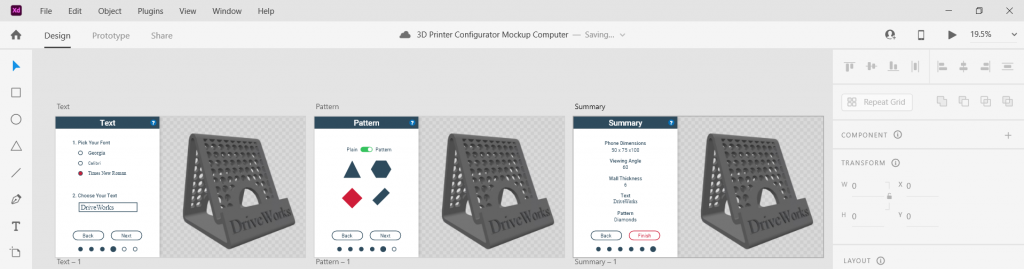
3D-Printing
Finally, Sophie printed some different configurations of the phone stand to check everything was working as it should.
At DriveWorks we have two 3D printers, an Ultimaker and a Formlabs printer.
Sophie decided to test how the phone stands would print using the Ultimaker 3D Printer and was very pleased with the results.
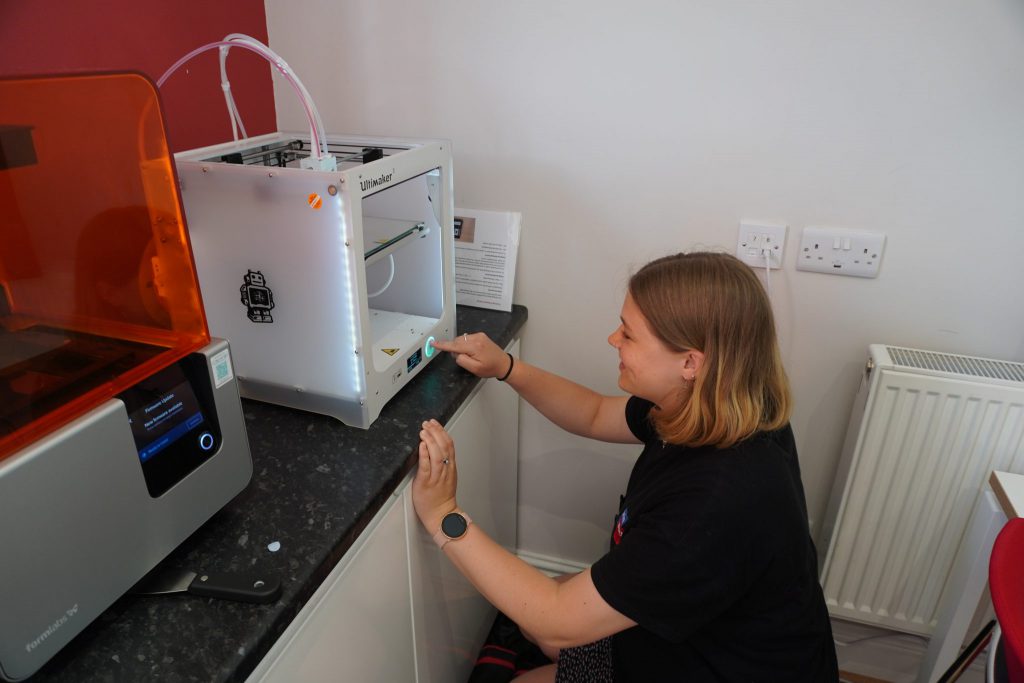
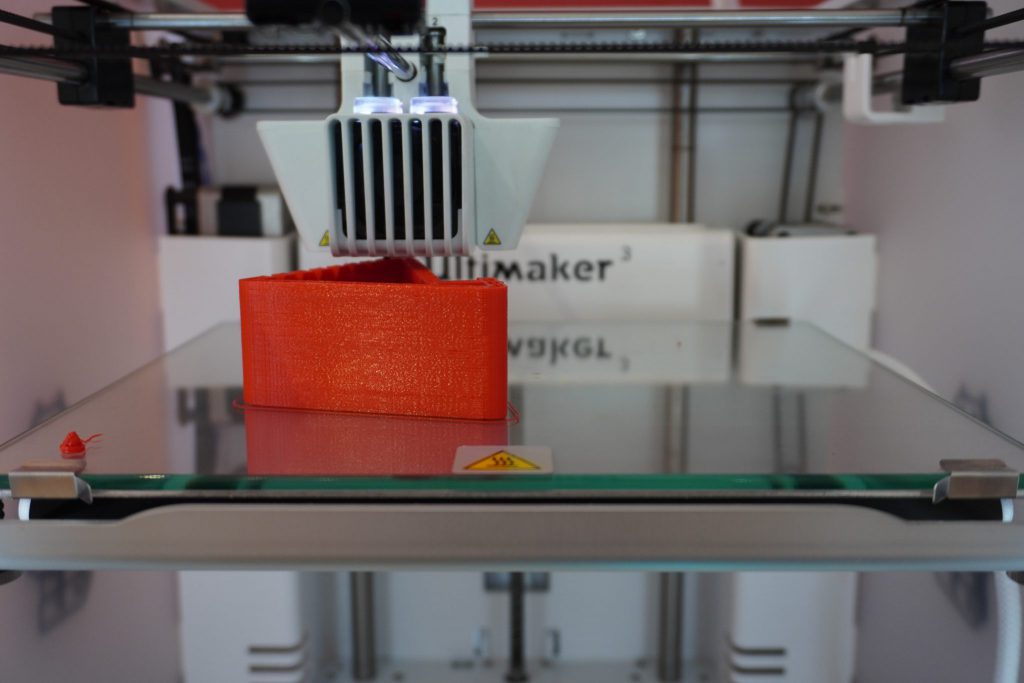
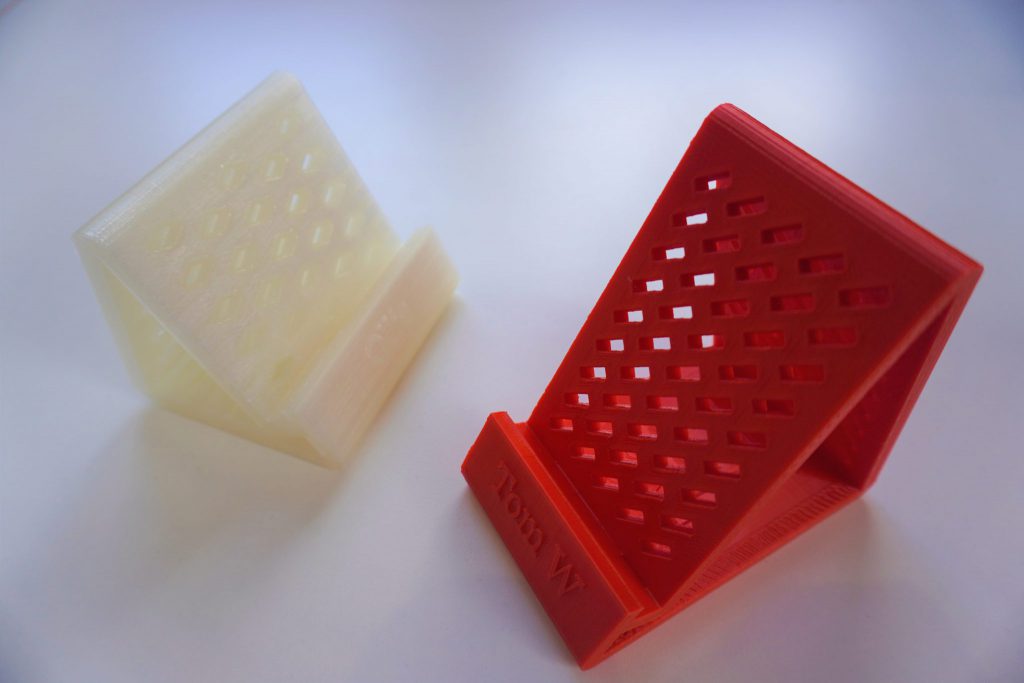