Embracing Technology for the Future of Manufacturing
Technology is driving the manufacturing industry forward and helping organizations to succeed.
Manufacturers who don’t embrace and plan for digital transformation will be left behind. As with any change, going digital can seem intimidating and scary. There are misconceptions that digital transformation is costly and time-consuming. There is often resistance from business leaders and employees, who fear making changes, despite the benefits it would bring.
The most important thing to embracing change is educating and understanding. Organizations that are well-informed about the possibilities of digital transformation are more likely to succeed. Educating yourself and your workforce about what digitization could mean for your company helps alleviate fears and debunk misconceptions.
The Fast-Paced World of Manufacturing
The manufacturing industry has changed a lot over time, with most of its evolution taking place in recent years. Advances in technology have revolutionized the way manufacturers design their products.
As technology moves faster, customer expectations rise as a result. Once mass production alone seemed impressive, but now customers demand custom output on the same grand scale.
Even in the last 3 years, the industry has changed massively. The Covid-19 pandemic accelerated technology in all aspects of life. Manufacturers turned to digital technologies to survive, and in some cases thrive, during and after the pandemic.
Manufacturing never stands still. Technology is, and will continue to be, a driving force behind the success of businesses.
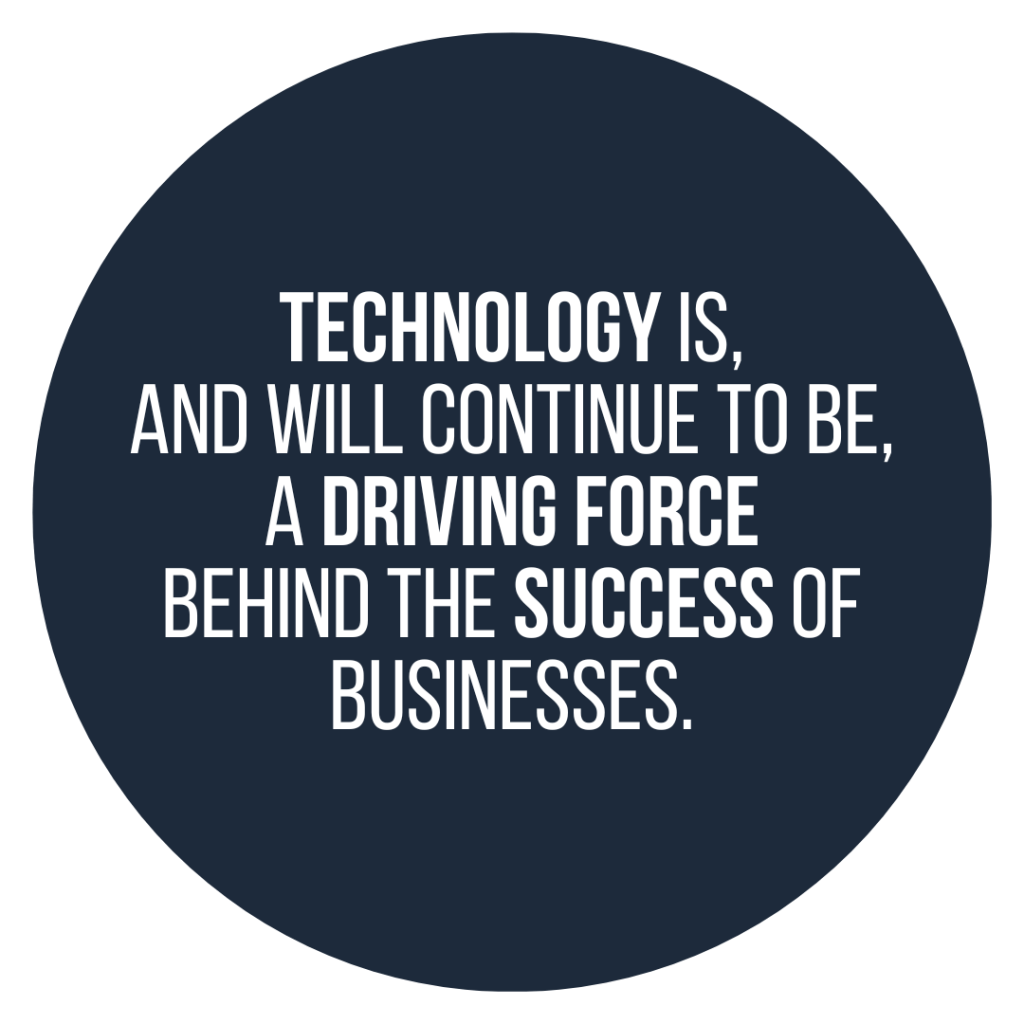
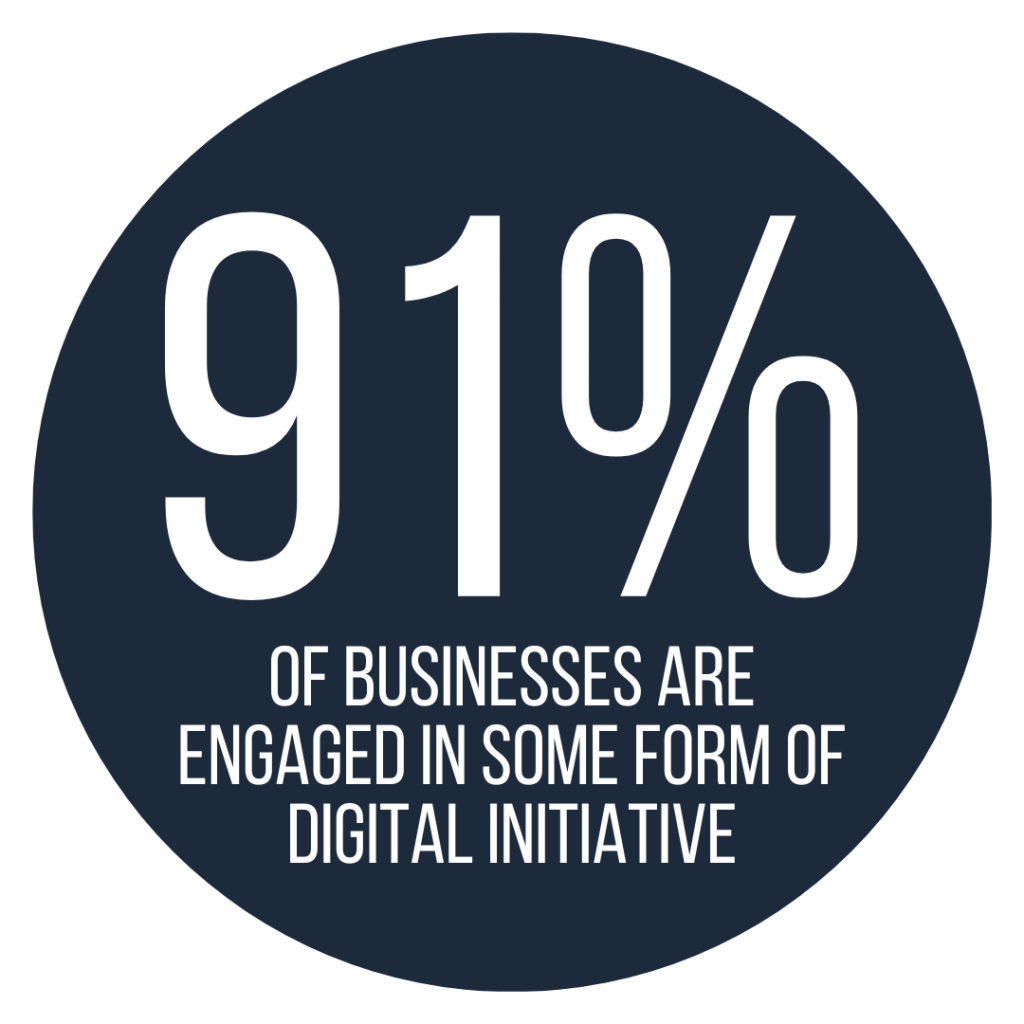
All Industries Are Turning to Technology
The need to adopt digital into your business is essential. Businesses are moving beyond just reaping the benefits of digitization, and are now seeing and embracing extra opportunities to excel at what they do.
There are historical examples of the success of embracing digital across many industries. Whilst Blockbuster stores closed their doors, Netflix dominated a new digital space. Uber have revolutionized the way we book and pay for taxis. Both have gone from strength to strength, finding a gap in the market and moving quickly to close it.
Digital is the future. It’s how companies can be agile to meet customer needs and expectations. It’s how business can do more with less whilst costs continue to rise.
According to Gartner, 91% of businesses are engaged in some form of digital initiative. Digitally transforming areas of your company are at the forefront of organizational growth.
Overcoming Resistance to Change
Whilst there are many benefits to digital transformation, resistance from employees is a common barrier to success. The fear of the unknown is sometimes too much, especially for those having to learn new skills. There are often fears around changing things that already work. Those who are comfortable with their current processes can be resistant to make changes and improvements.
There is also a misconception that digitizing areas of a company mean a loss of jobs. Digital technologies make monotonous jobs easier by freeing up employee time, enabling them to work more efficiently and dedicate time to more creative, valuable tasks.
Recognising this fear amongst employees is the first step to helping them overcome it. Employers should explain how technology can make the day-to-day tasks of their employees easier. Acknowledging fears makes employees feel valued and listened to.
Adopting new tools and technologies is the ideal opportunity for individuals to learn new skills, the valuable skills necessary for a future-ready workforce. Supporting employee shift to new ways of working is important to ensuring the success of digital transformation.
Employees can choose to embrace digitalization, learn it and use it, and become experts in it – or their skills will become outdated. Employees who embrace, learn, use and champion digital transformation are the ones who will carry skills that could accelerate their careers.
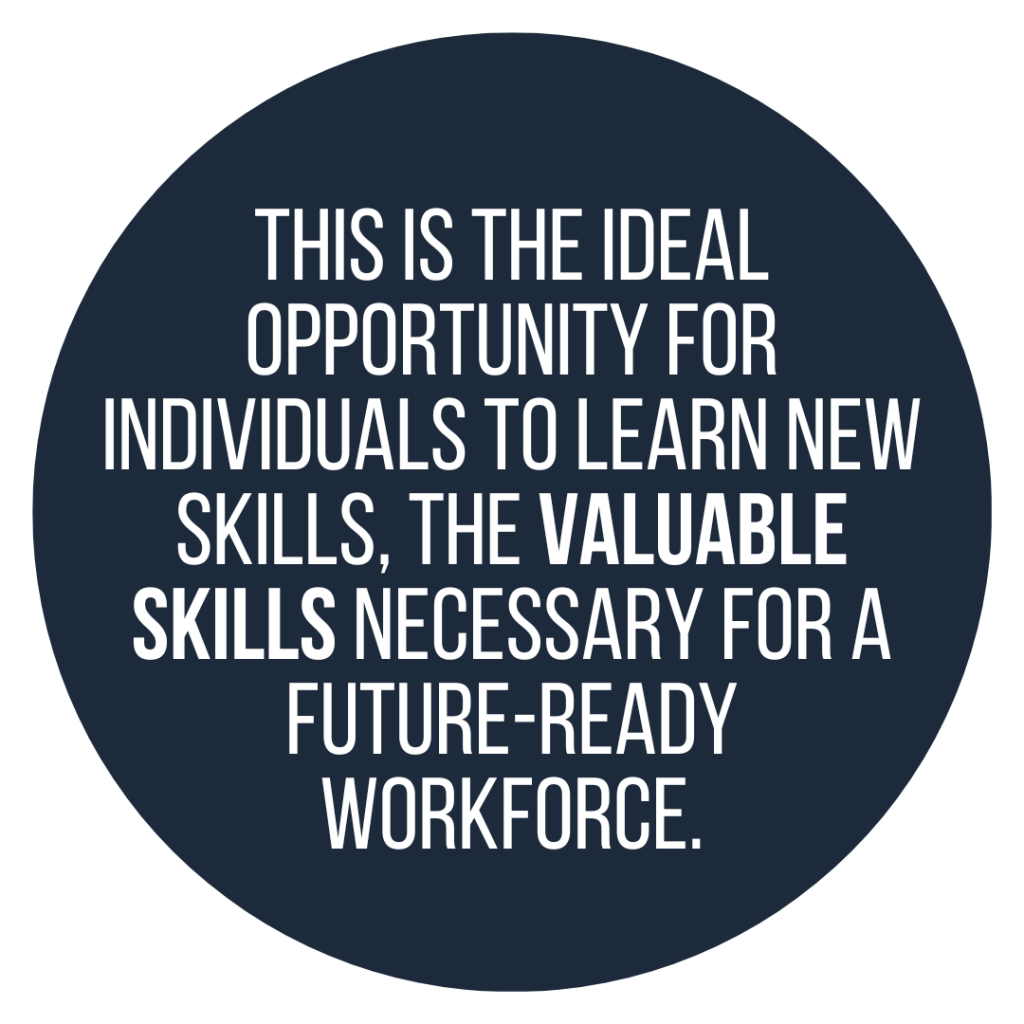
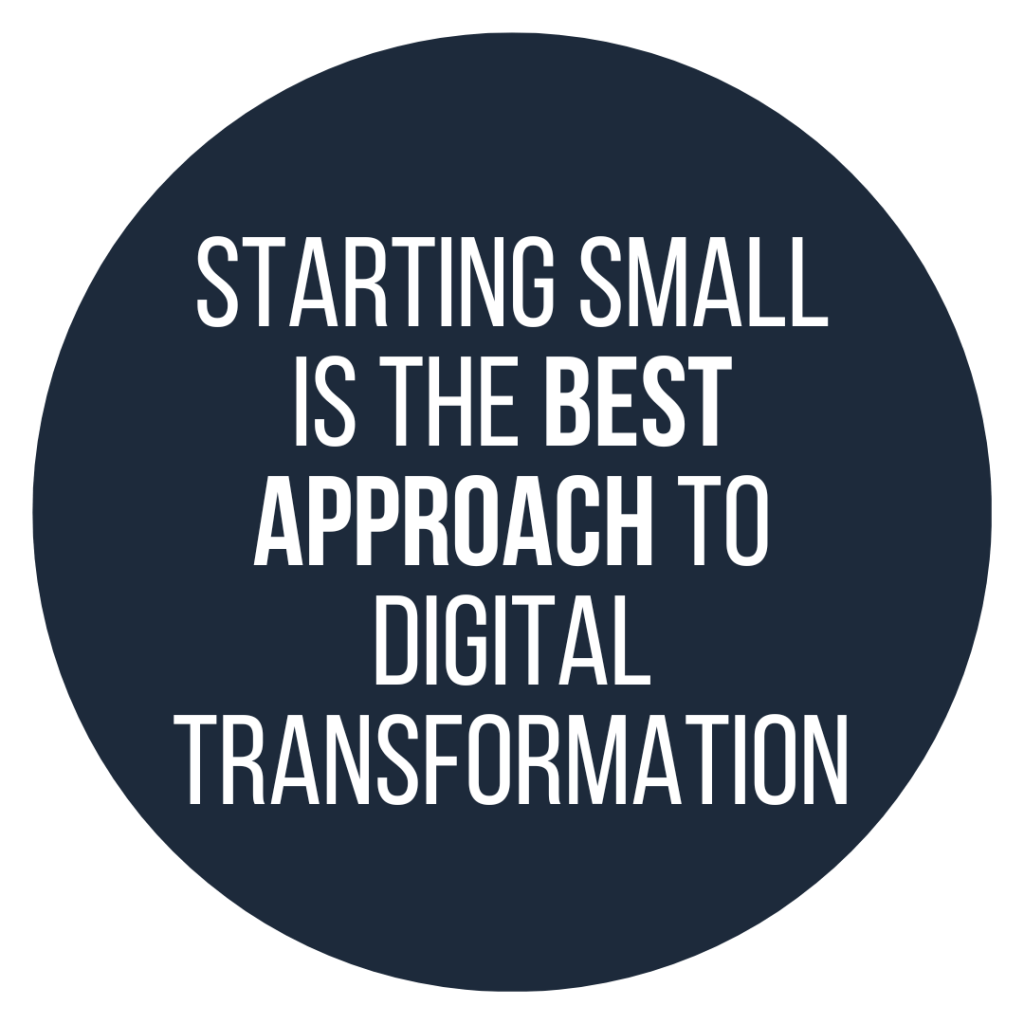
Testing Before Investing
One of the biggest misconceptions about digital transformation is the idea that absolutely everything will change all at once, and that workforces will have to adapt quickly to an entirely new way of working. Starting small is the best approach to digital transformation – it enables you to see how incremental gains can benefit your organisation while allowing employees to try and grasp technologies at a good pace.
Digital transformation doesn’t have to be expensive. A scalable approach is also more cost-effective. The incremental gains could feel like minor adjustments but once you’ve started to see the changes paying off, you can build on them to do more.
When planning out your approach to digital, it’s often difficult to know where to start and what will work. Look for free versions of a tool so you can try it out first and see how useful it is for you and your teams, test out features, and give you a head start on implementing a tool. Figure out what works for you, before committing to a tool and investing time and money.
You might even be able to do more with the existing technologies you already have – what technologies do you already have in your business? Are you using them to their full potential? Are there features and functionality you’re not using? Does one team use a digital tool that would also be useful for another team? Do you have access to additional tools that you’re not using? For example, if you have SOLIDWORKS, are there any Xpress products you could use? Xpress tools are available free with all SOLIDWORKS desktop licenses.
Improving Customer Experiences
This introduction of digital, like with previous revolutions we’ve seen in the manufacturing industry, creates benefits for businesses, and their customers.
Technology is changing the way consumers and businesses research and buy products. Digital technologies enable more immersive buying experiences. Customers can make changes, personalize options and visualize their selections. This detailed information eliminates costly and time-consuming changes later on in the process.
Automation means buying journeys are also faster and less prone to errors. Connecting data between company systems results in accurate pricing and delivery information. Order details can be sent directly to manufacturing, speeding up lead times and improving accuracy.
Customer expectations are higher than ever. Digital transformation enables organizations to meet rising customer demands profitably, without needing huge teams and budgets.
By meeting customer expectations with the help of technology, businesses will see how being more digital benefits all areas of the business. Satisfied customers increase retention, which keeps businesses thriving. Workforces can then see the value of digital and understand its longevity.
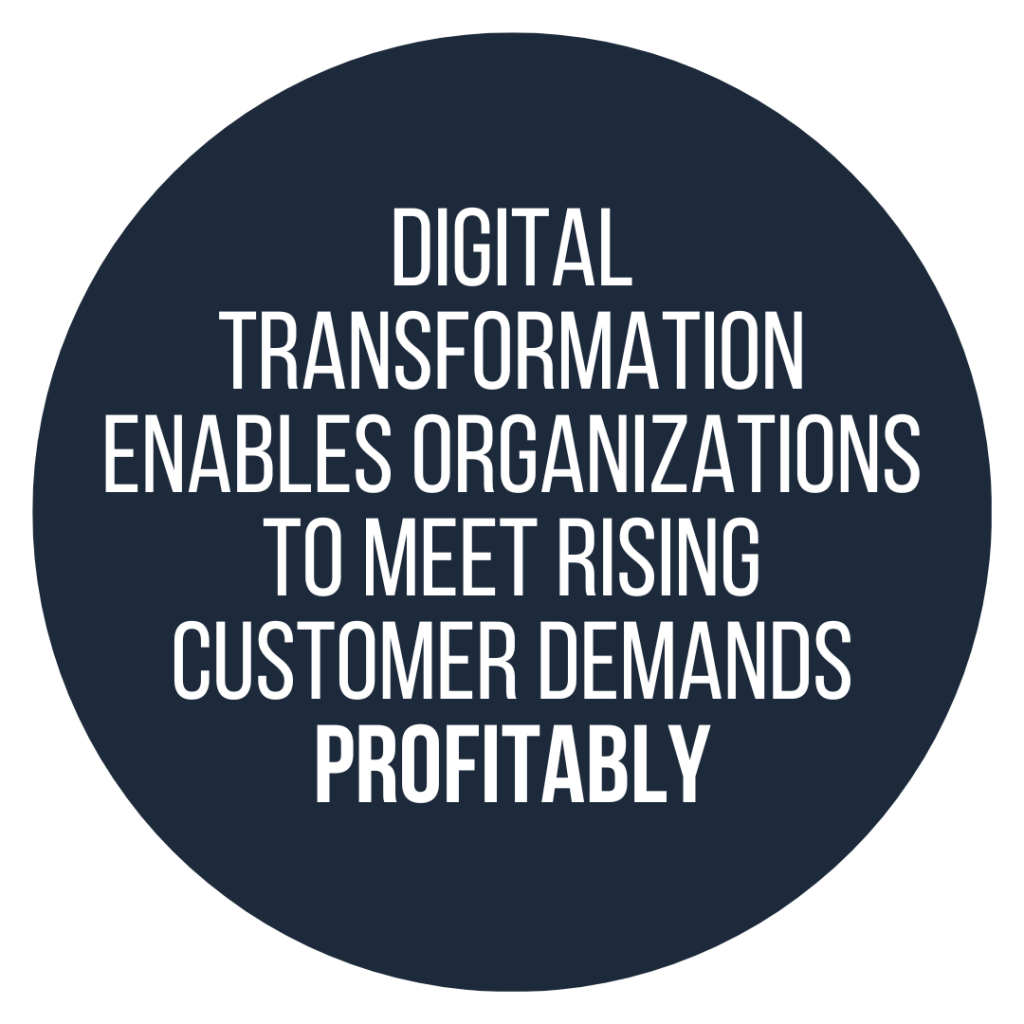
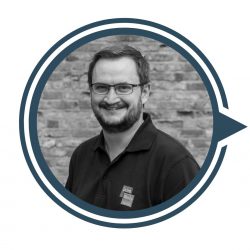
Dave Meecham
Technical Manager, DriveWorks
“During my time in industry I often encountered the phrase “but we’ve always done it this way”.
Overcoming this attitude is always a challenge, but without exception always worth the effort. Engineers want to create and innovate, embracing digital tools for the mundane same but different tasks provides the time for innovation.
Use this time to tackle those new concepts and ideas you’ve always had in mind “if only I had the time for this it could be fantastic!”
How are DriveWorks Customers Embracing Technology?
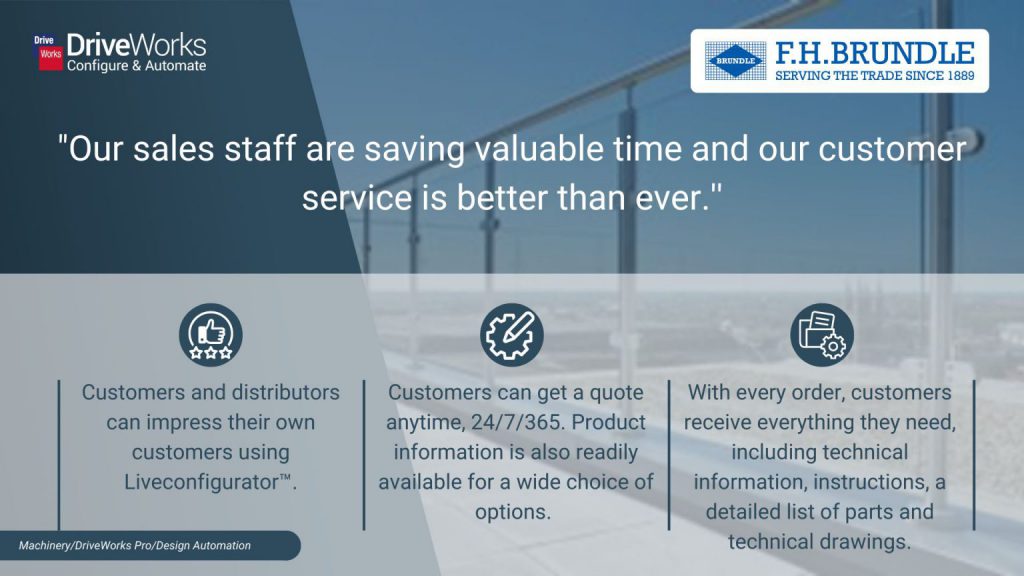
F.H. Brundle is a family-owned business, founded in 1889, they are wholesalers of steel products which includes a market-leading range of handrail and balustrade systems. F.H. Brundle stocks over 8,500 products, and new lines are continuously being added.
Since implementing DriveWorks, F.H. Brundle has benefitted by:
- Trade customers save time estimating, quoting and drawing
- Staff and customers automatically receive technical documentation
- They have developed Liveconfigurator, an online 3D configurator for their internal teams, distributors and customers.
- Customers can configure and get a quote anytime, 24/365
Find out more about how F. H. Brundle is automating with DriveWorks here.