Emerging Tech Trends in Manufacturing
The introduction of the new digital age has brought with it many modern manufacturing technologies, most of them specifically relevant to ‘Industry 4.0’ – the fourth industrial revolution, associated with automation, data exchange, digital technology, artificial intelligence and machine learning, and the ‘Internet of Things’.
Therefore, a lot of the manufacturing technologies innovating production and industry are also relevant to this fourth wave of technological advancement.
Over the past year, we have seen how the global pandemic has accelerated the adoption of digital. In particular, we have seen how this had affected manufacturers, forcing many to shift the way they think and use technology.
Results of a poll of several hundred U.S. manufacturing executives conducted by Deloitte in November 2020 found that more than three-quarters (76%) expect their companies to increase investment in digital initiatives, and to pilot and implement more Industry 4.0 technologies, in the year ahead.
In February, the Global Manufacturing & Industrial Summit released a report looking at trends that will dominate the manufacturing sector in 2021. The report explores how organisations are turning from crisis mode to recovery mode, as we continue to progress into the new year.
As part of this shift, the manufacturing industry is predicted to undergo huge changes during 2021.
Increased Investment In IIoT
One of the first trends the report looks at is Investment in Industrial Internet of Things. Though the Internet of Things (IoT) is becoming a more common, widespread technology in the manufacturing industry, it remains at the top of trends lists year after year for its adaptability and innovation – Hitachi Solutions
The Internet of Things (IoT) has the potential to connect and monitor operational components with unprecedented ease and efficiency. The digital connectedness of the manufacturing process enables organisations to continuously modify and improve their processes using accurate, real time data that will aid efficiency, reduce waste, and improve the overall quality of products.
For instance, using smart sensors, remote supervisory control and data acquisition, IoT is able to drive industrial advancement by improving safety, streamlining manufacturing and delivering cost savings on record levels.
Taking this concept further, the Industrial Internet of Things (IIoT) will become a major element of Industry 4.0, enhancing mobility, flexibility and resilience on an unparalleled level. The IIoT has the potential to transform traditional, linear manufacturing supply chains into dynamic, interconnected value chains that can incorporate ecosystem partners in a more interconnected way, driving industrial connectivity, productivity, and performance across the world.
As a result of this potential, Forbes expects more than $267 billion to be invested globally in IoT technology over the next five years, with the majority of the investment being made in manufacturing, transportation, and logistics.
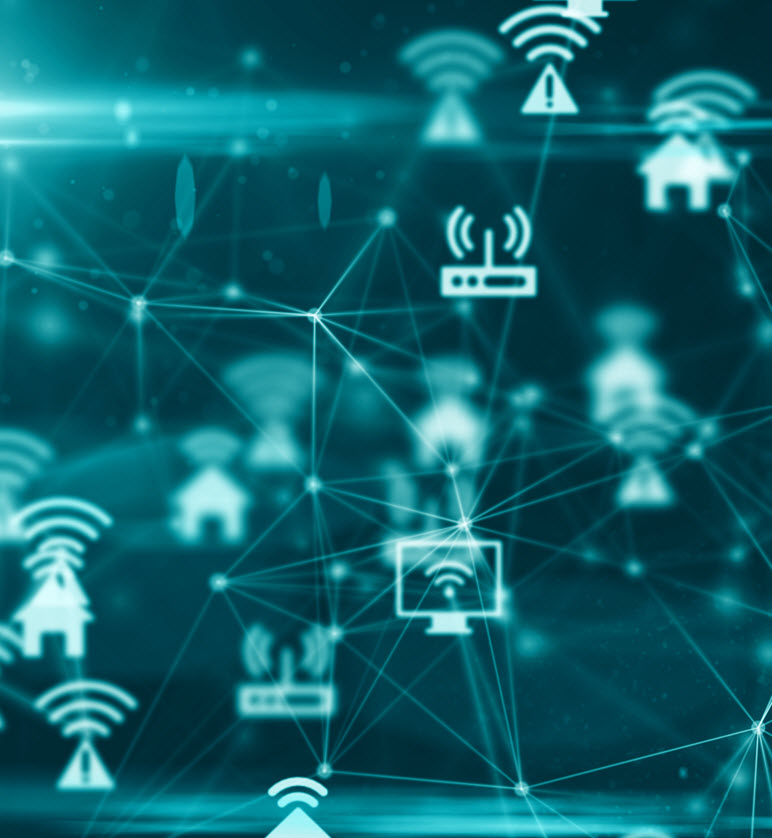
Glocalisation
At the start of January 2021, Forbes took a look at Manufacturing Tech Trends To Look For In 2021. One of the key trends pointed out by Forbes was the ‘Move to Glocalisation’.
Glocalisation is the combination of the words ‘globalisation’ and ‘localisation’. It is a term that is used to describe a type of business that has been seeing more and more growth, a type of business that is distributed globally but adjusted to meet local needs as well.
Due to the effects of the pandemic on international borders and business travel, Forbes predicts that many companies will focus on balancing localised and globalised business options in order to stay competitive.
The Global Manufacturing and Industrialisation Summit (GMIS), and leading professional services firm, PwC, launched a report outlining the 2021 key global trends that will enable manufacturers to succeed at glocalisation. The report highlights that companies must regionalise their footprint, increase the use of robotics for manufacturing and logistics, and change the cost model for production and sourcing.
The report states that amid these emerging themes, COVID-19 has ensured that the case for moving from global to ‘glocal’ operations has gained significant momentum. Reflecting on various global perspectives where the pandemic has accelerated efforts by industrial companies to make inflexible global footprints more agile and responsive to demand.
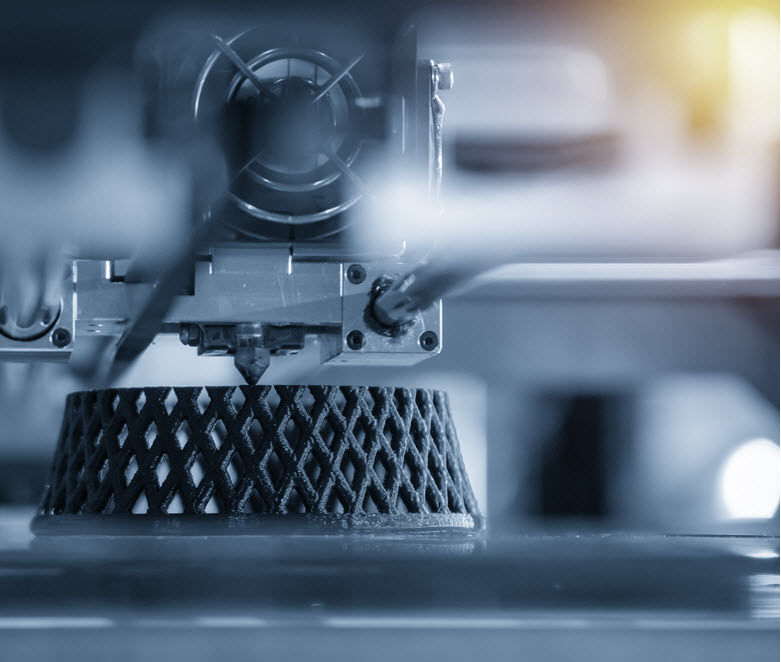
A Surge in 3D Printing
Another trend reported by Forbes is a ‘Surge in 3D Printing’. According to the Association of Supply Chain Management, COVID-19 gave the world “a glimpse into how 3D Printing can be used temporarily to alleviate the strain on supply chains during demand surges and shortages, as it did with medical equipment.”
In May 2020, we looked at How Manufacturers Are Pulling Together in the Fight Against COVID-19 and how 3D Printing played a huge role in this. We saw how manufacturers were rapidly switching and upscaling production through the use of 3D Printing. Complex parts could be made anywhere with the power of advanced digital design and 3D Printing.
“The supply chain disruptions of 2020 pushed many companies to radically rethink their design & manufacturing strategy,” says Brad Rothenberg, founder and CEO of 3D Printing software company nTopology.
Inventors are combining 3D Printing with traditional processes creating unique combinations of parts that perform better with lower cost that can be manufactured closer to the customer, all while being more sustainable.
Robotics
Back to the GMIS report on trends that will dominate the manufacturing sector in 2021, and another focus is on Robots and Cobots.
As reported by BeeKeeper.io ‘Robots on the factory floor are growing at warp speed thanks to their declining cost and increasing capabilities’.
The pandemic saw a huge uptake of factory robots, with companies of all sizes leaning on automation to keep their factories running. Digital insights site, Diginomica believes that in 2021, cobots will no longer be a pandemic-inspired experiment, but a critical necessity to sustain required automation and output throughout the year.
According to the International Federation of Robotics, there are a record 2.7 million industrial robots operating in factories worldwide, with robotic shipments up 41% over 2018, particularly in non-automotive workplaces. These figures are likely to grow in 2021.
Robotics allow faster production by reducing the risk of human error or injury, increasing the speed of production, and their systems can be updated as soon as the technology becomes available. As a result, incorporating robotics into manufacturing processes allows organisations to reduce costs and waste, all whilst improving quality.
Collaborative robots (cobots), automated guided vehicles (AGV), autonomous mobile robots (AMR), intelligent logistics, and robotic sorting systems are likely to see high levels of demand in 2021. These robotic and automation systems are expected to grow along with the recovery in logistic, warehousing, packaging, and semiconductor sectors.
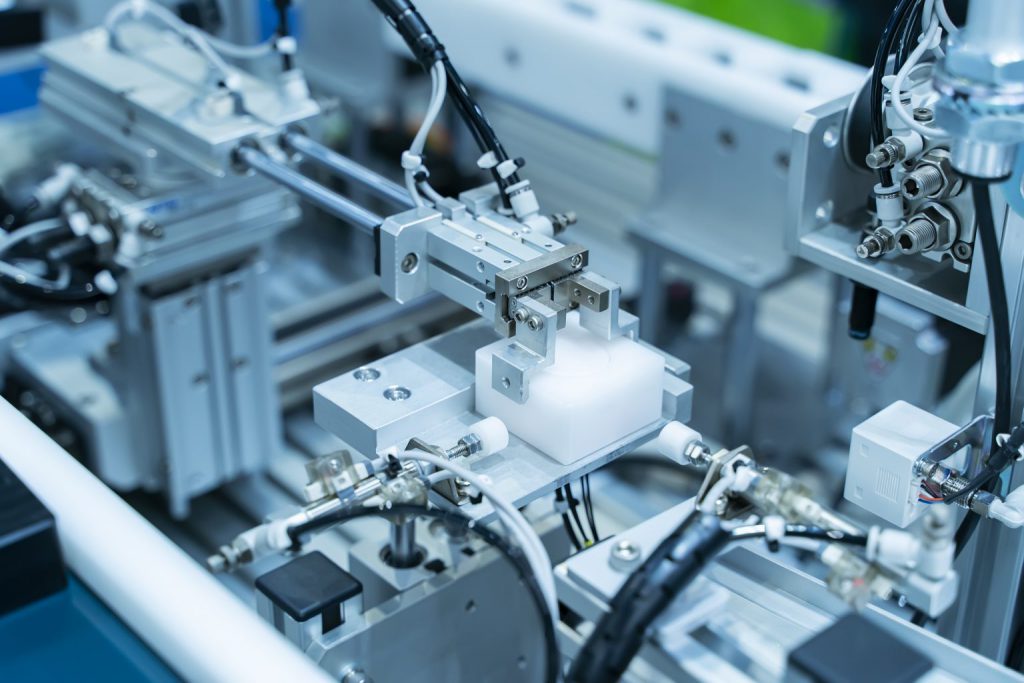
Automation
Automation in manufacturing is not a new concept, but the level of adoption and its application has boomed over the past ten years. The wider availability and lowering cost of implementing automation has allowed cutting-edge automation technology to reach more areas of the sector and throughout the world, and as a consequence, automation is changing the way manufacturers ‘make’.
With manufacturing automation, organisations are reducing costs, optimising workflows, and increasing their bottom line. It is a critical trend that will only grow as more companies along the value change adopt this approach.
Forbes report that despite the doomsday headlines of years past, it’s clear by now that automation is not just replacing existing work but instead, creating new work.
Digital Connectivity
Supply Chain Technology
In 2020, the manufacturing and food processing industries were severely impacted by the global pandemic. From closed facilities to rigid communication channels, it was difficult for some to remain flexible. As a result, 94% of Fortune 1000 companies experienced disruptions in their supply chain.
In 2021, digital connectivity will be one of the dominating trends in manufacturing and food processing. Businesses will be looking to digitally connect as many aspects of the production process as possible to stay ahead of further disruptions.
Digital Transformation on the Factory Floor
The pandemic reminded manufacturers about the fragility of relying on labour, access to physical space, and centralised factories halfway around the world to produce goods.
Fortunately, advanced technology – sensors, machine learning, computer vision, robotics, cloud computing, edge computing, and 5G network infrastructure – has proven to increase supply chain resiliency for manufacturers who adopt it, reports Forbes.
Digital Twins
According to Deloitte’s 2021 Manufacturing Industry Outlook report, Digital twin technology could support new levels of resilience and flexibility in 2021, and can help prepare manufacturers for any future disruptive events.
Deloitte’s poll of manufacturing executives identified that 24% of executives who plan to invest in digital technologies believe digital twin technology will be the most important technology in which their company will invest in 2021 (tied for first with augmented workforce efficiencies).
Using a digital twin, a manufacturer can virtually recreate a product, its production, and even simulate its performance in the real world without having to “bend metal” or take any other physical action.
Digital twins offer a wide range of benefits, including increased productivity, by reducing development time for new products and avoiding costly defects. But perhaps the greatest opportunity for digital twins in a post– COVID-19 world is their ability to enable the flexibility and agility that manufacturers may need to respond to the unknowns of the constantly shifting “new normal”.
Edge Intelligence
Forbes report that in 2021, agility will be critical. For example, collaborative robots, require manufacturers to become better equipped to respond to changing situations, since cobots make real-time, complex decisions during the task they work on with humans.
To get there, computing power and data processing must shift to the “edge,” or closer to where the data is being created, in order to reduce latency and boost processing.
“Moving to the edge will protect the safety and security of the workforce,” says Flavio Bonomi, board advisor to Lynx Software Technologies. “At the same time, it helps manufacture goods in a more agile, efficient manner.”
According to the IDC Data Age report ‘The Digitization of the World’, by 2025, 175 zettabytes (or 175 trillion gigabytes) of data will be generated around the globe and edge devices will create more than 90 zettabytes of that data.
Edge computing is a distributed computing model in which computing takes place near the physical location of production, rather than on a centralised server or in the cloud.
In manufacturing, edge computing resources can include machines, gateways, protocol converters, or other types of industrial controllers.
Most often in manufacturing, edge computing refers to the use of a dedicated edge device.
It is game-changing for the manufacturing sector as by distributing computing resources, manufacturers can improve data processing speed, filter signal from noise early, and improve data accessibility.

Try DriveWorks Solo for free
Get instant access to DriveWorks Solo for 30 days. No credit card required.