Rolmaster Conveyors create customized and cost-effective conveyors using DriveWorksXpress.
Since 1946, Rolmaster Conveyors has been designing, building and maintaining cost-effective conveyors and speciality handling equipment for a wide range of industrial manufacturing sectors. Their range of products includes roller belts, chain or wire mesh conveyors, complex lifts, turntables and transfer systems, which are all manufactured at their facility in Ontario, Canada.
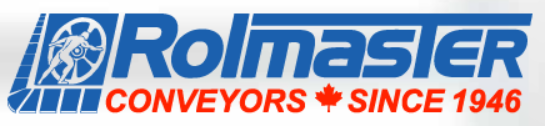
They started using SOLIDWORKS in 2004 and DriveWorksXpress in 2008. Paul Del Net, Senior Engineer at Rolmaster talks about the productivity gains using DriveWorksXpress…
“A new template for a new conveyor standard will take me a few days once all the modelling is done and verified for use with DriveWorks”
It used to take Paul between 30 – 45 minutes to create a variation of a design. By using SOLIDWORKS and DriveWorksXpress, it now takes Paul “20 seconds to enter the data and 5 minutes to print”.
Due to the nature of the product being automated within DriveWorksXpress, the number of variations that can be produced is unlimited. As DriveWorksXpress is included within every seat of SOLIDWORKS, projects can be shared with other colleagues who use the software. Rolmaster Conveyors found this useful as it made the flow of work within the company seamless and more time effective.
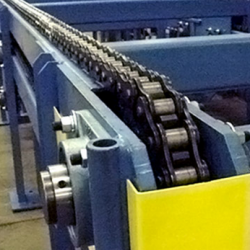
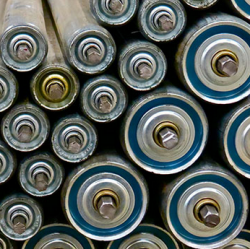
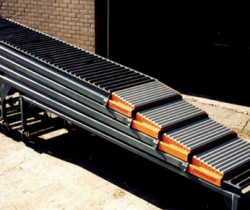
Due to the impressive results Rolmaster Conveyors saw using DriveWorksXpress they have now upgraded to DriveWorks Pro to take advantage of the advanced functionality within the software.
Time saving metrics
Previous system = 30 – 45 minutes
DriveWorks = 25 seconds