Wozair Limited are based in the South of England and specialize in the design and manufacture of high integrity heating, ventilating and air conditioning (HVAC) equipment for the Renewables sector.
Earlier this year, members of the DriveWorks team took a trip down to their offices to meet with Wozair and their DriveWorks reseller Visiativ UK, to find out more about how they use DriveWorks.
Working Smarter & Staying Ahead of the Competition with DriveWorks
Implementing DriveWorks has enabled Wozair to automate and streamline their design process, reduce their risk of human errors, and improve communication between their design and manufacturing teams.
They’ve also been able to gain additional accreditations, ensure material traceability, and harness the expertise and knowledge of their design engineers.
Achieving a Faster Turnaround with DriveWorks
Wozair credit DriveWorks technology with giving them a “fresh start”. Implementing DriveWorks has enabled them to automate and speed up their design process, reduce their risk of human error, and get information from their design team to their manufacturing team much quicker.
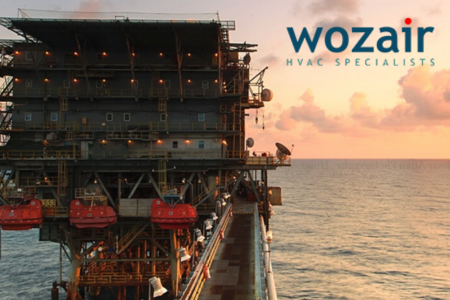
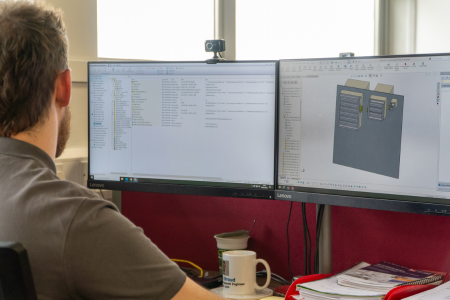
Less Manual Input and Streamlined Processes
Before using DriveWorks, Wozair relied on an outdated Excel-based Integrated Design System to produce their .dxf and BOM files. Implementing DriveWorks has led to a reduction in the number of manual inputs required and allows them to get the design information through to manufacturing in a shorter space of time.
Quicker Project Set up and Material Traceability
Wozair’s sales team use their DriveWorks configurator to generate manufacturing details.
Their engineers are self-taught and they are now able to add new products to their DriveWorks implementation every 2-3 months.
Before DriveWorks, creating drawings for their products was a time consuming, manual process, this is now done in minutes using DriveWorks.
Material traceability during the manufacturing process is vital in the industries Wozair serve. This is achieved, with the help of DriveWorks, by etching markings onto their cut parts.
Wozair has also achieved additional accreditations as a result of the improvements made to their processes, and they have been able to document and share the knowledge of their most experienced engineers.
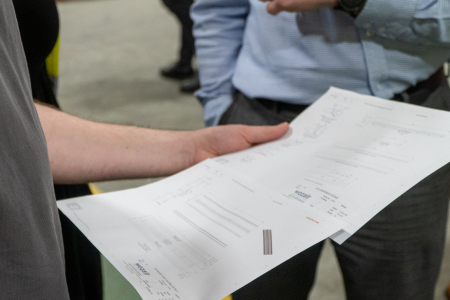
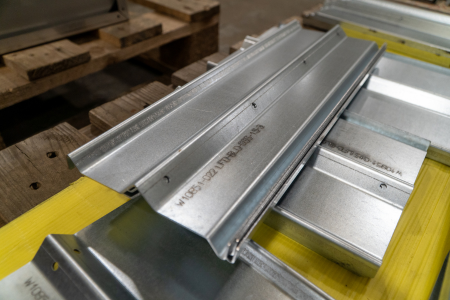
“DriveWorks allows us to get from the design stage, to a finished product in the shortest possible time – giving our clients the best delivery program and distinguishing our performance from our competitors.”
– Alistair Brooks
Principle Engineer at Wozair Ltd
DriveWorks Customer Stories
DriveWorks design automation, product configuration and CPQ software is used by companies of different sizes from a range of industries all over the world.
Sharing customer stories enables you to see how our software solutions help companies save time, reduce costs, and improve productivity by automating repetitive design tasks and enabling greater flexibility in product customization.