Designing the Perfect Gift
Every year, we recognise our SOLIDWORKS User Group Leader of the Year for their work going above and beyond to support the SOLIDWORKS Community. This year was no different, so while in Nashville at 3DEXPERIENCE World our team presented this years winner – Betty Baker with the award.
Along with the award we also proudly presented Betty with her very own personalised bottle opener – designed in SOLIDWORKS, configured in DriveWorks and 3D printed.
The Design Process
Amer, placement student at DriveWorks, was given the task of designing something we could configure, produce and give away at events, Amer began researching, brainstorming and sharing ideas with our tech team.
Amer decided on a 3D printed bottle opener and began to design the bottle opener in SOLIDWORKS. With each design, Amer considered how the bottle opener would perform in action.
Firstly, he considered the feasibility of printing the design on a 3D printer. Would the designed model be suitable for the 3D printer and how long would it take to print?
He then considered the usability of the product, would the design be strong enough to withhold the pressure or could it buckle and break?
He also thought about the style of the bottle opener, what size should it be and what design would be most comfortable to hold?
After creating a number of prototypes, Amer decided on a final design.
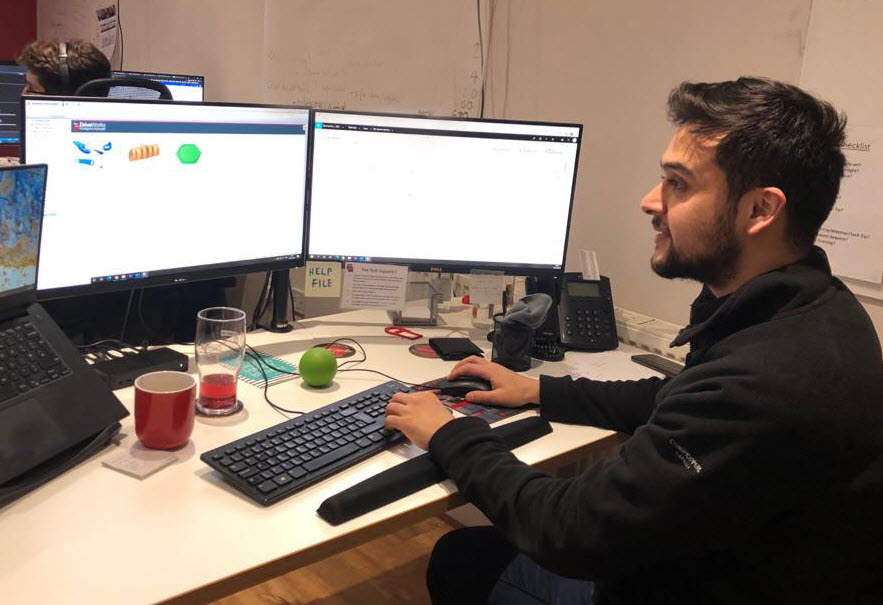

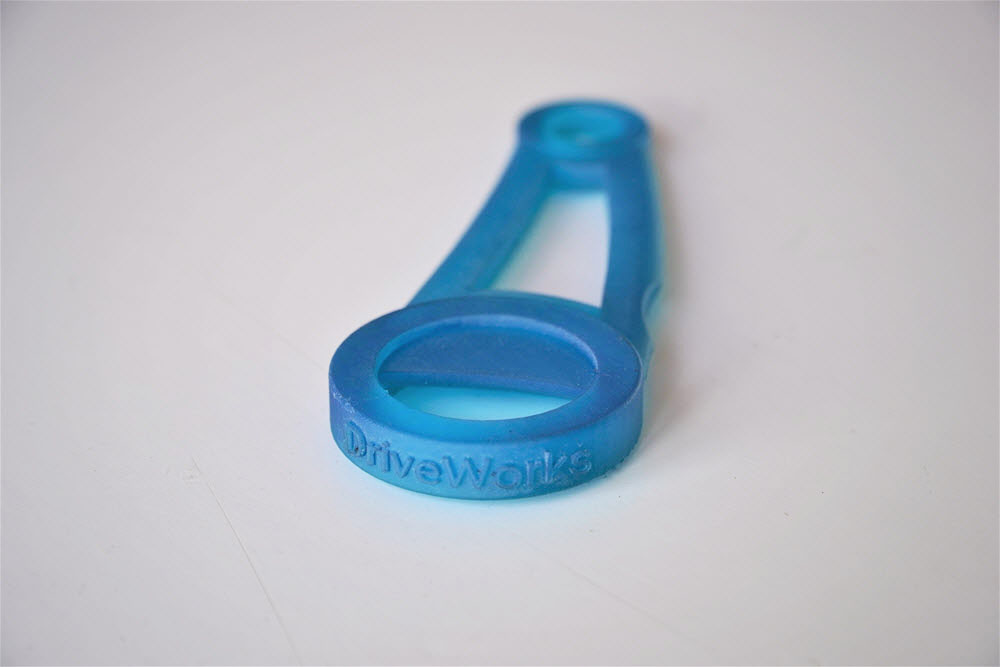
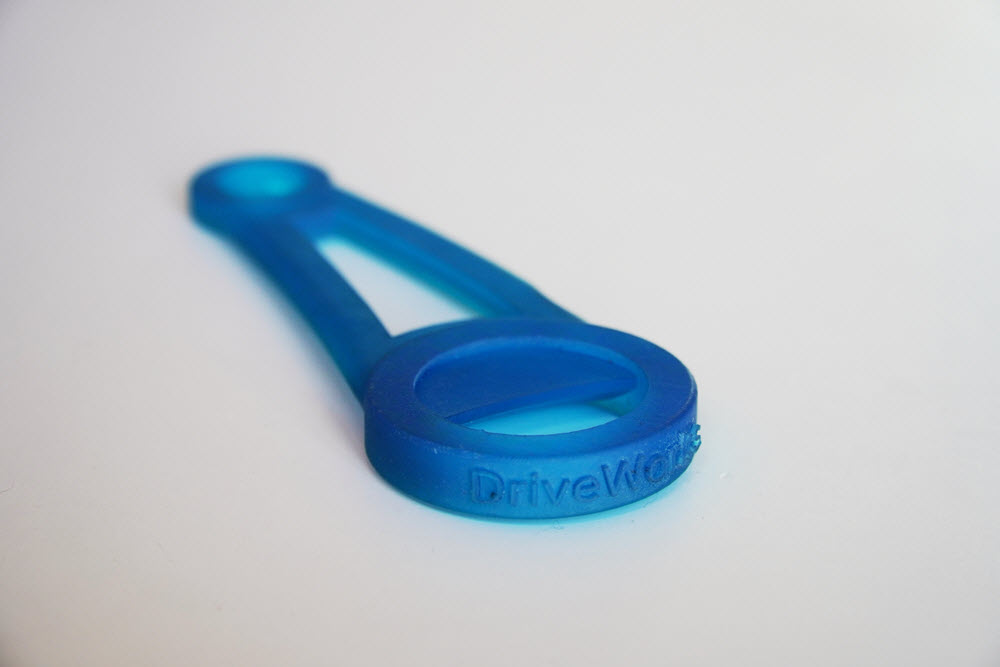
Creating the Configurator
With the product decided, Amer then went on to create a DriveWorks Configurator for the bottle opener.
With the configurator Amer has designed, it’s easy to follow the user interface and configure a custom bottle opener, making selections based on the user’s preferences.
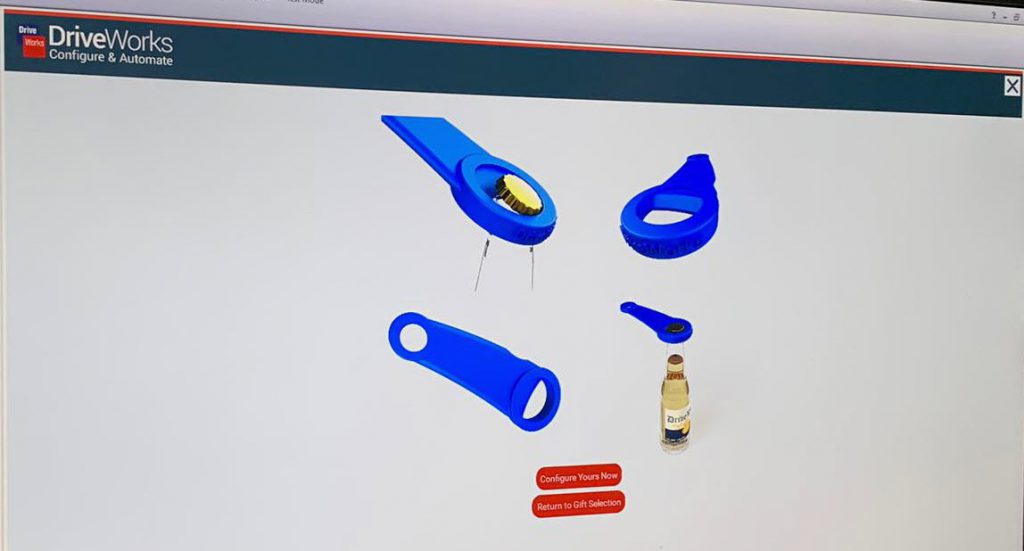
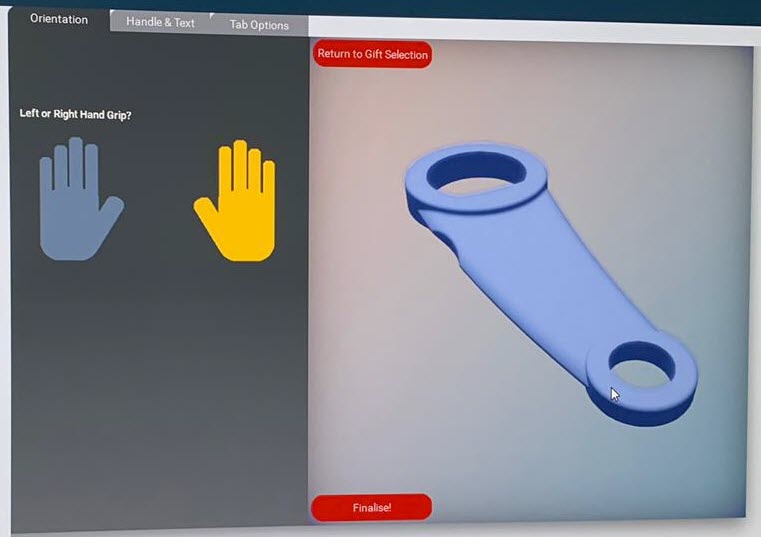
Left or Right Handed?
The orientation option allows users to select a right-handed or left-handed bottle opener.
With standard bottle openers, it’s normally a one size fits all.
However, Amer wanted our bottle opener to be more personal and work best for everyone.
When the user selects left or right handed, the configurator switches the bottle opener round so the grip is in the right place.
Choosing a Handle
Next the user moves onto choosing the handle style of thier bottle opener.
There are 3 different options to choose from:
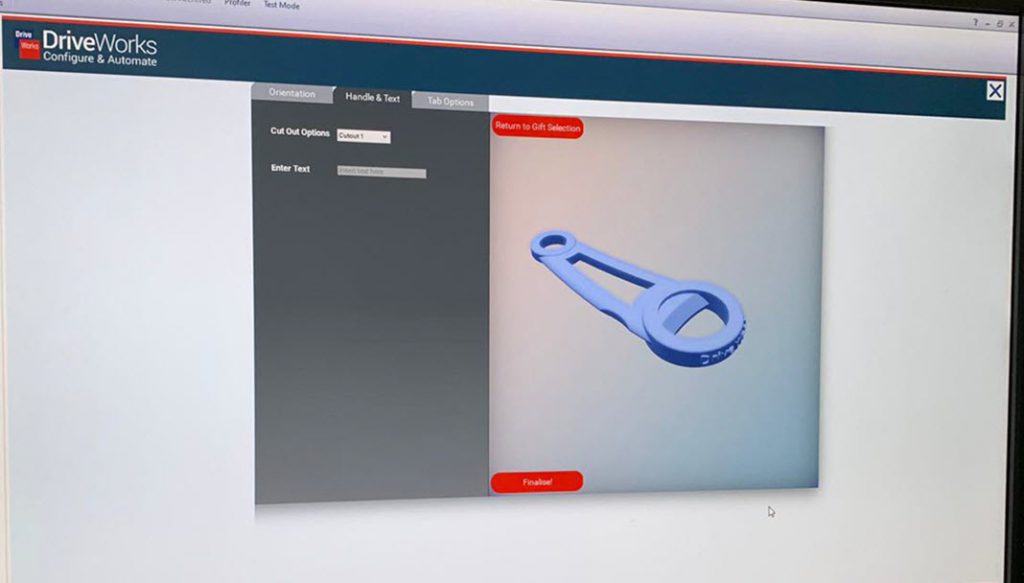
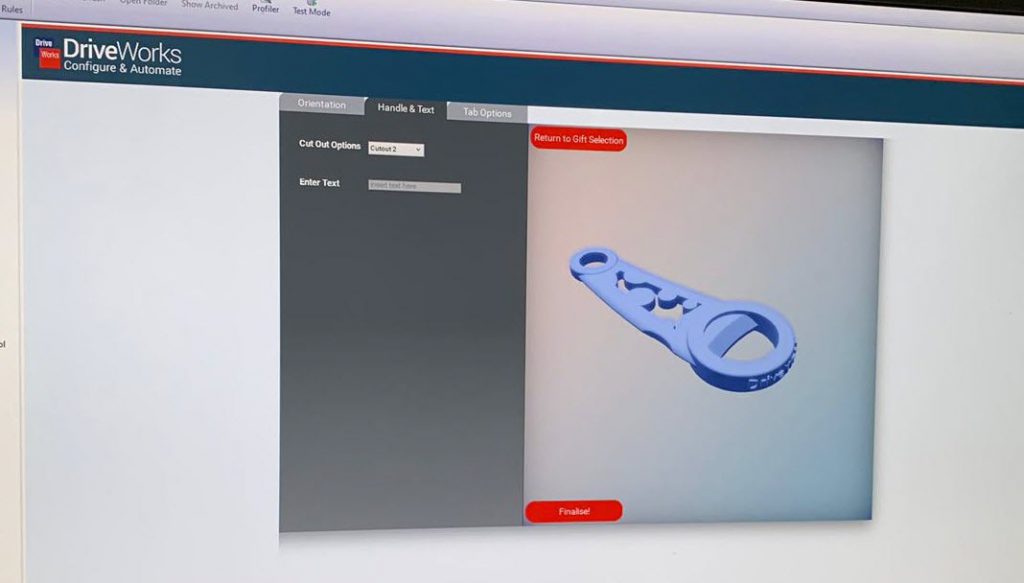
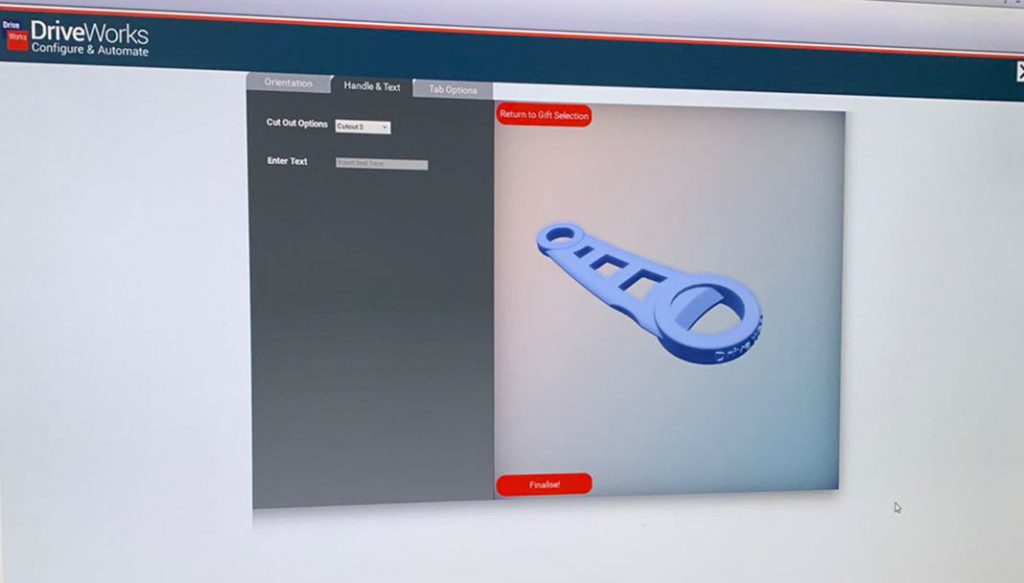
Push or Pull Open?
Users can also choose how the bottle opener will work.
Amer created the different options for push and pull by changing the direction of the tab inside the bottle opening circle.
In this section of the configurator, Amer also added a slider so the user can offset the location of the tab, moving it to their preferred angle for opening.
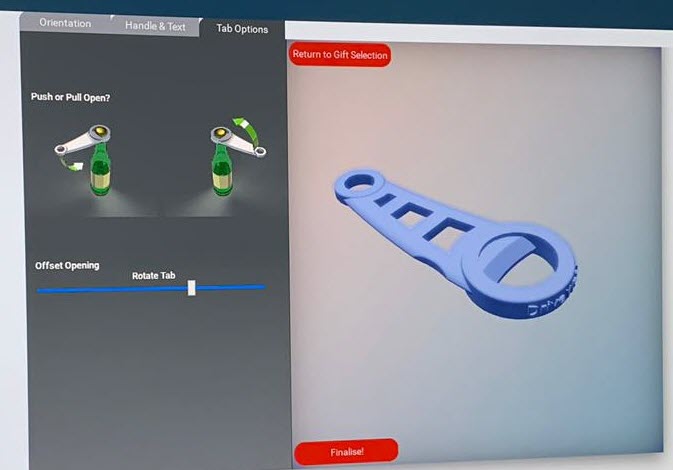
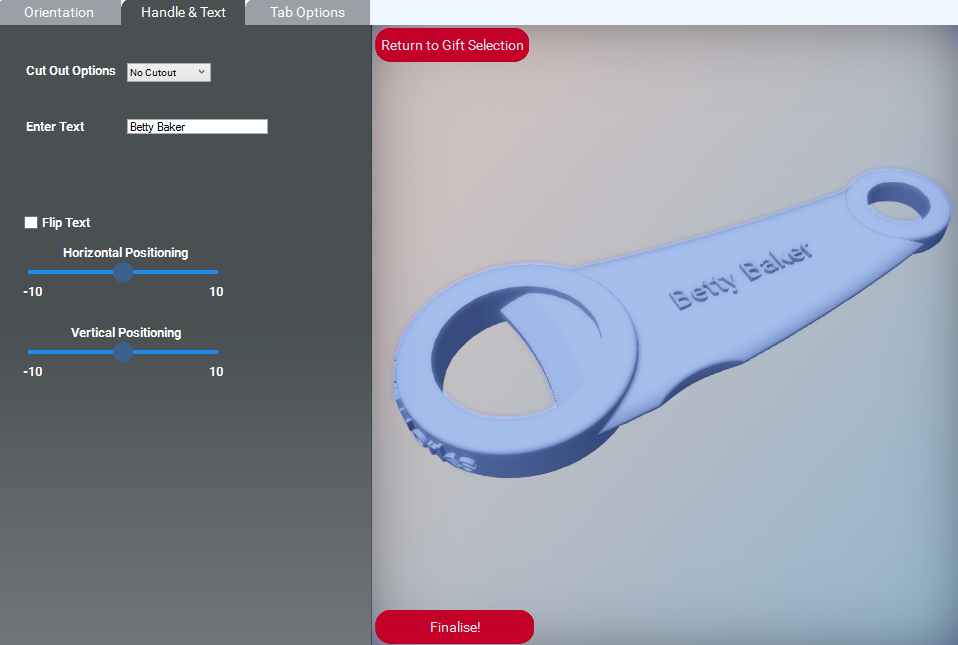
Making it Personal
In true DriveWorks style, Amer didn’t want this to be just any 3D printed bottle opener.
Alongside the personalised configurator options, Amer also added the final feature of adding text to the bottle opener.
This makes the gift personal and unique.
Automated Emails
Once the bottle opener has been configured, users are taken to a form to fill out their details. DriveWorks then sends an email to the user with the details of all their personalised configurator options.
Attached to the email is an STL file to send the bottle opener to a 3D printer without the need to have SOLIDWORKS installed.
Of course, all of this was done in DriveWorks – using the latest functionality in DriveWorks 18.
3D Printing
The next step is printing the final design. Here at DriveWorks we have two 3D printers, an Ultimaker and a Formlabs printer. Amer printed on both printers to decide which would work best for his bottle opener design.
Amer found it worked best printing on the Formlabs printer which took 7 hours for the bottle opener to print.
Once the printer had finished, Amer removed the part from the plate and began the process of cleaning the bottle opener. First the model goes into an ethanol bath to wash any excess resin off. Then the support structures are taken off ready to go in the curer.
In the curer, the bottle opener was exposed to UV light and 60-degree heat. This strengthens the crosslinks in the polymer structure to improve the strength, stiffness, and temperature resistance. It also gives the bottle opener its frosty finish.
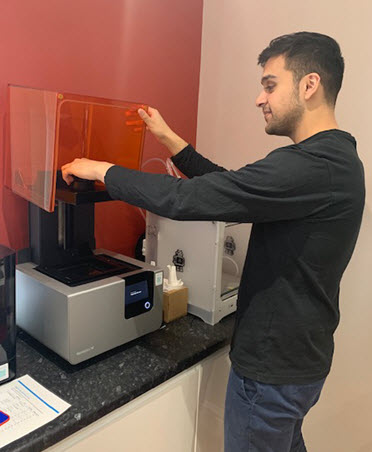
Presenting Our Gift to Betty Baker
While we were at 3DEXPERIENCE World we proudly presented our the DriveWorks Award for SOLIDWORKS User Group Leader of the Year to Betty Baker.
Betty received a certificate and her own personalised 3D printed bottle opener.
We also showed Betty how her bottle opener was designed, personalised and 3D printed.
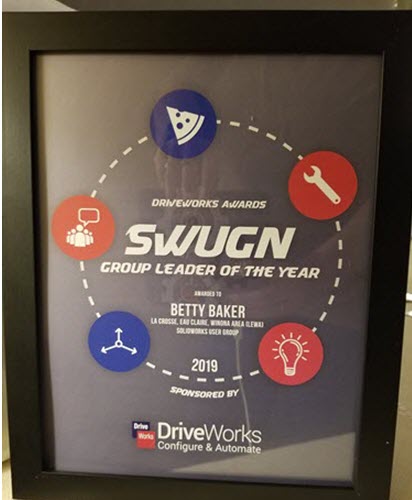
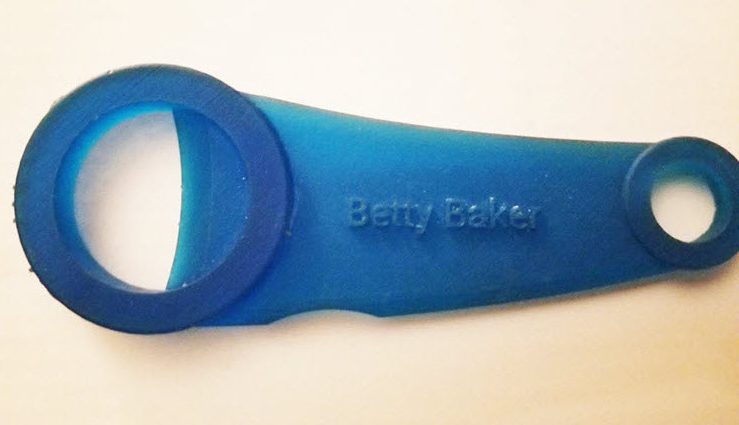
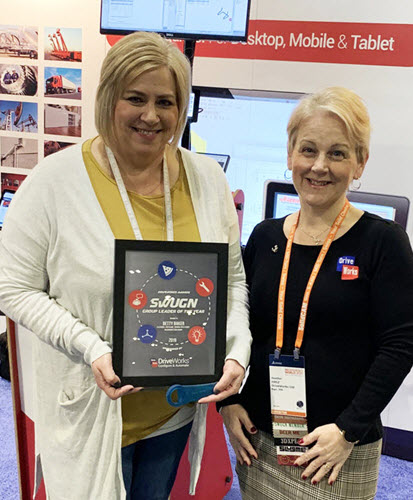
More Personalised Products
Since creating the bottle opener configurator, Amer has created more configurators within the project. Now we can also configure, personalise and print 3D printed coasters and cable holders.
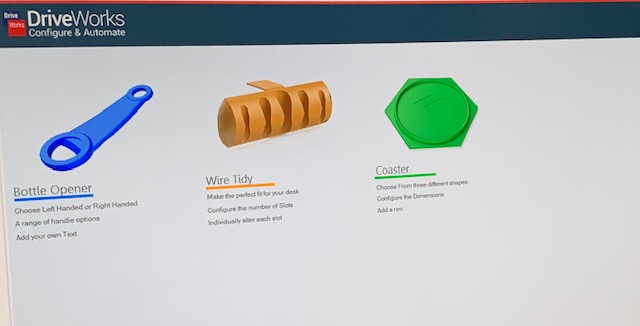
Have a go with one of our configurators!
Explore our industry examples on our online demo site driveworkslive.com
See what’s possible with DriveWorks and how versatile the software is.