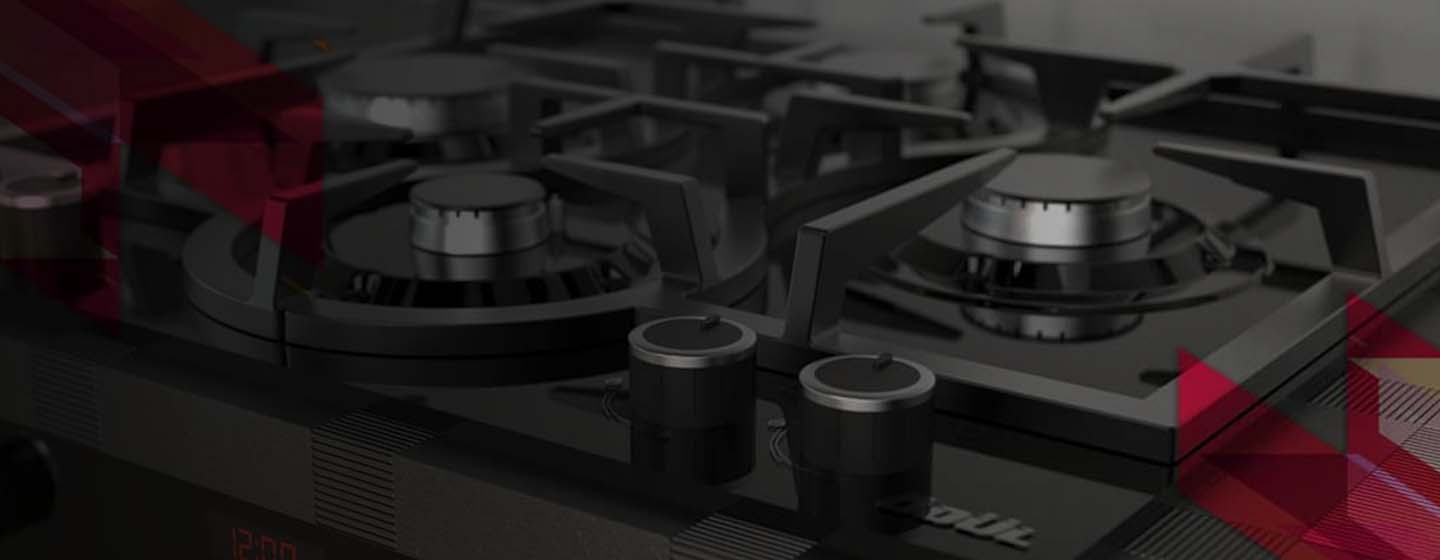
Ödül Madeni Eşya
Ödül Madeni Eşya has reduced configuration time by 40% and cut design time by 70% with DriveWorks Pro
Challenge
Ödül’s existing process used a pre-designed excel spreadsheet to input the details of each order. This was prone to errors and relied on the sales team sharing files with appropriate teams individually.
Solution
Ödül have built an online product configurator using DriveWorks Pro, enabling both their sales team and their customers to configure products accurately and efficiently.
Results
DriveWorks has enabled Ödül to prevent the wrong product from being manufactured whilst also reducing the time spent specifying new products by 40% and reducing labor time by 70%.
Company overview
ÖDÜL MADENİ EŞYA, based in Turkey, has been a manufacturer of home appliances for more than 50 years, exporting to over 86 countries around the world.
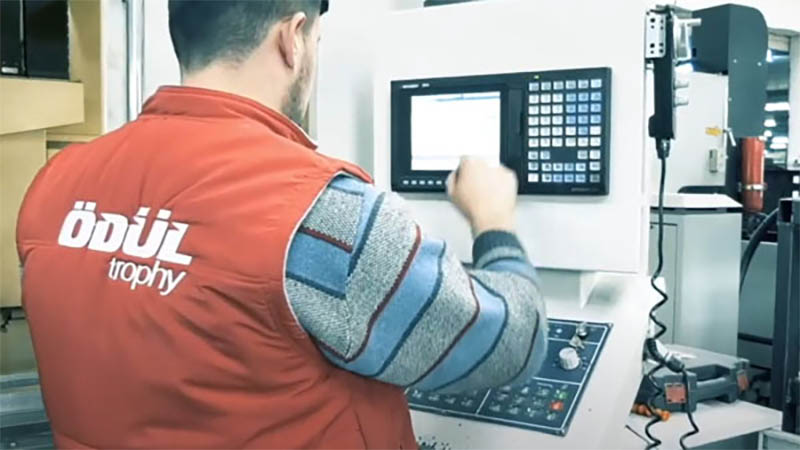
Challenge
Streamlining processes
Before implementing DriveWorks, the sales team at ÖDÜL used a pre-designed excel spreadsheet to input the details of each individual order. Completed forms were then manually sent to the relevant department within ÖDÜL via email.
This entire process relied on members of their sales team manually sending files to the appropriate teams individually, leaving room for error.
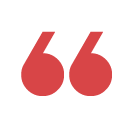
Our customers can configure products whenever and wherever they want, regardless of time, place, or device!
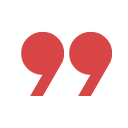
Murat Saçmaci – Chairman
Ödül
Solution
Saving time, improving customer experience
Ödül chose DriveWorks Pro software to build an online product configurator for their internal sales team and customers to configure products accurately and efficiently.
Using DriveWorks, Ödül collects all the required information from each individual specification, such as product details, delivery times, payment & delivery terms. Once collected, this information is automatically shared with Ödül’s ERP system.
Our customers can configure products whenever and wherever they want, regardless of time, place, or device!
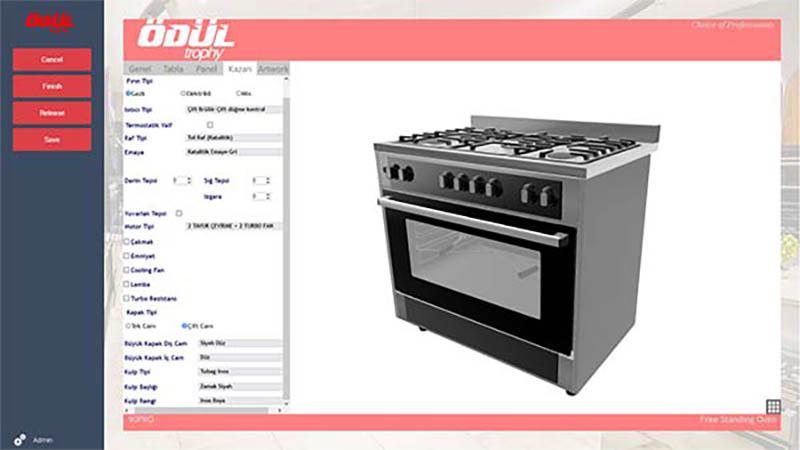
Results
Preventing the wrong product from being manufactured
When speaking about the benefits of DriveWorks for their customers, Murat Saçmaci, Chairman at Ödül said “order and customer data is now collected from a single source, DriveWorks, which limits errors and significantly reduces time spent collecting order information from customers.”
All the documents related to each specific order, such as technical drawings, manufacturing documentation and purchase orders are created, then sent to the relevant department within Ödül.
For Ödül, the most important aspect of DriveWorks is that it prevents the wrong product from being manufactured.
Adding DriveWorks to their design process has also reduced the time spent specifying new products for their customers by 40% and reduced labor time by 70%.
Try DriveWorks Pro configurator examples online
Request a demo with a technical specialist
Fill out the form below and a member of the DriveWorks team will be in touch.